Aluminum alloys are widely used materials in modern manufacturing and construction. Its lightweight, high strength, and good corrosion resistance make it one of the first choices in many applications. Among many 6005 aluminum vs 6063 materials have attracted much attention due to their unique performance characteristics.
Aluminum alloys are widely used in industry and construction, and 6005 and 6063 aluminum alloys are two of the materials that have attracted much attention. There are some differences between the two in terms of composition, properties, and applications, so understanding the differences between them is crucial to making the right choice of the right material. In this article, we will provide an in-depth comparison of 6005 aluminum alloy and 6063 aluminum alloy, detailing everything from chemical and physical properties to applications and costs.
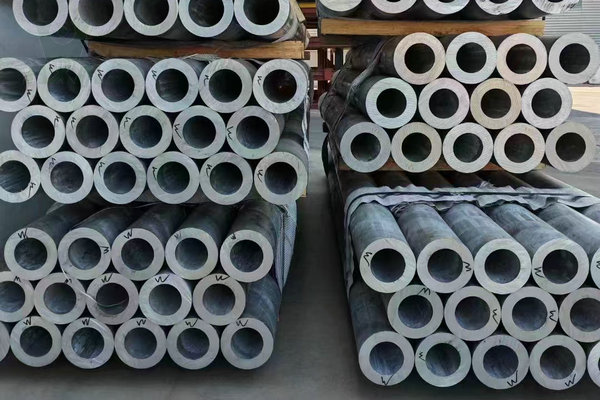
Understanding the differences between 6005 aluminum suppliers, 6063 aluminum manufacturers, and aluminum stock options can help businesses and buyers make informed purchasing decisions. If you are looking for 6005 aluminum or 6063 aluminum at competitive prices, this guide will help you choose the right alloy.
What is 6005 Aluminum Alloy?
6005 aluminum alloy is an aluminum-silicon alloy whose main alloys are aluminum, silicon and manganese. This alloy has excellent strength and corrosion resistance, making it suitable for a variety of industrial applications and excels especially in building and structural applications.
If you are searching for 6005 aluminum manufacturers, stock availability, or price quotes, feel free to contact us for more details.
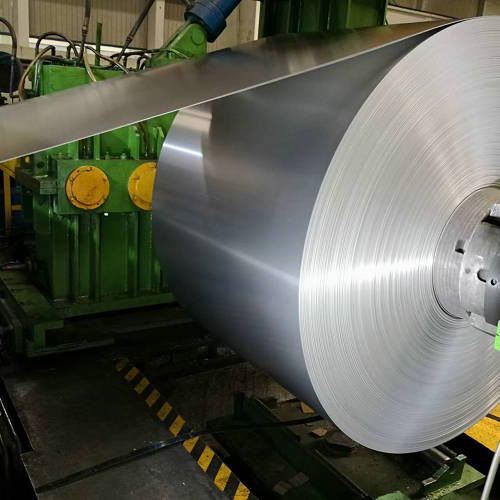
What is 6063 Aluminum Alloy?
6063 aluminum alloy is also an aluminum-silicon alloy whose main components include aluminum, silicon and magnesium. This alloy is widely used in construction and manufacturing due to its good processability and corrosion resistance.
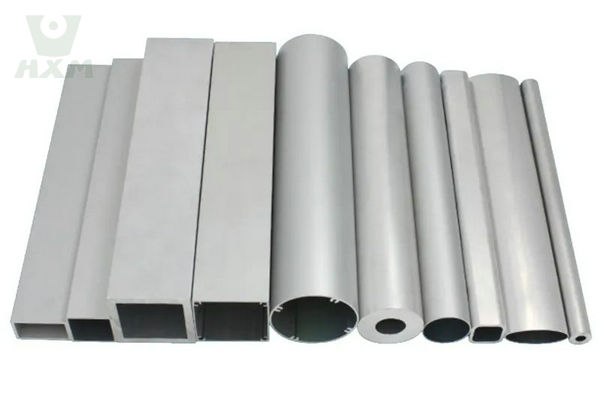
6063 Aluminum Alloy
6063 Aluminum Alloy Suppliers | Manufacturer | Factory Welcome to Huaxiao Metal Company, you deserve the best quality 6063 aluminum alloy products! Aluminum alloy 6063
If you are looking for 6063 aluminum suppliers, large inventory and competitive prices, we provide high-quality aluminum products to meet your needs, please feel free to contact us for any 6063 aluminum product information you need!
The Difference Between 6005 Aluminum vs 6063
Let’s compare 6005 aluminum vs 6063 from different perspectives, including composition, mechanical properties, cost, application, etc.
Chemical Composition of Aluminum 6005 vs 6063:
here is the comparison of the chemical composition between 6005 and 6063 aluminum alloys, presented in a table format:
Element | 6005 Aluminum Alloy | 6063 Aluminum Alloy |
---|---|---|
Al | Over 97.9% | Over 98.6% |
Si | 0.6-0.9% | 0.2-0.6% |
Fe | Below 0.35% | Below 0.35% |
Mn | 0.4-0.9% | Below 0.1% |
Mg | 0.4-0.7% | 0.45-0.9% |
Cu | Below 0.1% | Below 0.1% |
Zn | Below 0.1% | Below 0.1% |
Ti | Below 0.1% | Below 0.1% |
This table outlines the approximate range of major elements in the 6005 and 6063 aluminum alloys. It’s important to note that specific alloy compositions may vary by manufacturer, and this table represents a general overview. When selecting an alloy, it is advisable to refer to the specific material specifications and data provided by the aluminum manufacturer.
Mechanical Properties of 6005 Aluminum vs 6063:
Here is a table outlining the key mechanical properties comparison between 6005 and 6063 aluminum alloys:
Mechanical Properties | 6005 Aluminum Alloy | 6063 Aluminum Alloy |
---|---|---|
Tensile Strength | High | Medium to High |
Yield Strength | Medium to High | Medium |
Elongation | 10-12% | 8-10% |
Hardness (HV) | 140-160 | 70-105 |
Density | 2.7 g/cm³ | 2.7 g/cm³ |
This table summarizes the major mechanical properties of 6005 and 6063 aluminum alloys. It’s important to note that these values can vary based on specific heat treatment conditions, material thickness, and other factors. When selecting the appropriate aluminum alloy, consideration of the specific mechanical requirements for the intended application is essential.
Cost of 6005 Aluminum vs 6063:
The price of 6005 aluminum is usually slightly higher than that of 6063 aluminum because it has stronger mechanical properties and is suitable for high-load structures.
However, the specific price is affected by market conditions, specifications, quantity, surface treatment and other factors. It is recommended to contact us directly for the latest quotation!
Contact us now to get a quotation for 6005 and 6063 aluminum alloy, and learn about inventory status, product information, etc.!
Characteristics of Aluminum 6063 vs 6005:
The characteristics of aluminum alloys 6063 and 6005 distinguish them in terms of their properties and applications. Here’s a brief overview of the key characteristics of each alloy:
Aluminum 6063:
Formability and Extrudability: 6063 aluminum is highly formable and extrudable, making it well-suited for various shaping and manufacturing processes.
Surface Finish: It provides a smooth and glossy surface finish, making it popular for applications where appearance matters, such as architectural elements.
Strength and Hardness: While 6063 offers good strength, it is generally not as strong as some other aluminum alloys like 6005. However, it compensates with excellent corrosion resistance.
Corrosion Resistance: 6063 aluminum exhibits good corrosion resistance, making it suitable for outdoor and marine applications.
Weldability: It has good weldability, allowing for ease of joining in various fabrication processes.
Applications: Commonly used in architectural and construction applications, window and door frames, railings, and extruded structural components.
Aluminum 6005:
High Strength: 6005 aluminum alloy is known for its high strength, particularly in the heat-treated condition. It is suitable for applications requiring enhanced structural integrity.
Weldability: While still weldable, 6005 may require more attention to welding parameters compared to 6063 due to its higher strength.
Corrosion Resistance: Offers good corrosion resistance, although not as corrosion-resistant as 6063.
Machinability: It exhibits good machinability, facilitating various machining processes.
Applications: Used in structural applications, such as bridges, building frames, and other instances where high strength is a primary requirement.
Cost: The cost of 6005 aluminum alloy may be relatively higher compared to some other alloys due to its enhanced strength characteristics.
In summary, while both 6063 and 6005 aluminum alloys are versatile and widely used, they differ in their strength, formability, and specific applications. The choice between them depends on the specific requirements of the intended use, considering factors such as strength, appearance, and cost.
In Conclusion:
Both 6005 and 6063 aluminum alloys are excellent materials, and the choice depends on the specific application needs. 6005 is more suitable for structural applications that require a certain degree of strength and weldability, while 6063 is more suitable for applications that require high appearance requirements and extrusion processing, such as building doors, windows, and decorative materials. When choosing a suitable aluminum alloy, you need to consider the material’s performance characteristics, production process, and specific application environment.
No matter which alloy you need, we have 6005 aluminum in stock, 6063 aluminum in stock, and competitive pricing to meet your requirements.
Contact us today for the latest 6005 aluminum and 6063 aluminum pricing, stock availability, and bulk orders!