Aluminum Foam Manufacturers
Aluminum foam is an excellent material that combines versatility, durability and efficiency. As a leading aluminum foam supplier and manufacturer, Huaxiao Metal is committed to providing first-class aluminum foam panels, tubes and other products to meet your needs. Contact us today to get a foam rate quote or learn more about our aluminum foam.
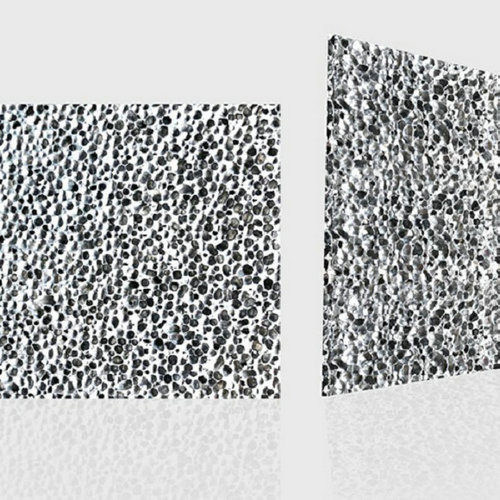
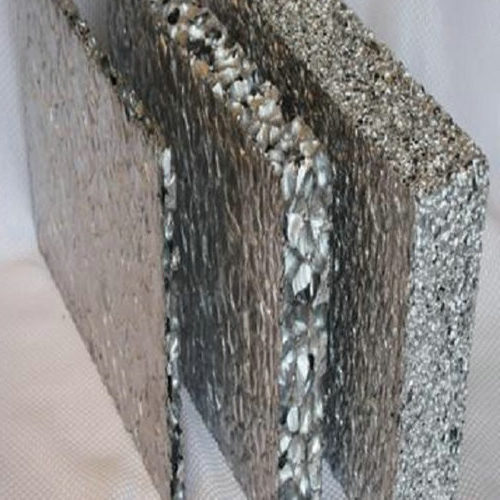
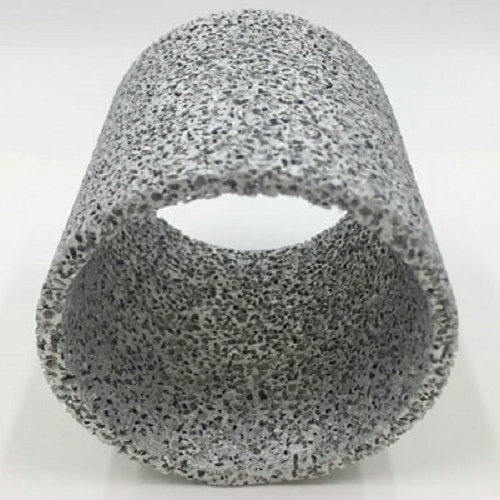
Aluminum Foam Price, please free to contact us.
Aluminum metal foam is an innovative material that features lightweight structures and excellent mechanical properties. Made from aluminum metal infused with a foaming agent, this unique material combines strength, durability and lightweight components, making it ideal for a variety of industrial applications. Contact us for more information:
- Aluminum Foam Prices
- Stock Availability
- Custom Options
Aluminum Foam
Aluminum Foam Suppliers | Aluminum Foam Manufacturers
Huaxiao metal company has more than 60 independent intellectual property rights and more than 10 invention patents; it creates ultra-high-power continuous electromagnetic shielding technology and provides core technical support for scientific research equipment (controllable nuclear fusion test device EAST “artificial sun”); The Olympic Hockey Hall provides architectural decoration materials. Products are widely used in aerospace, bulletproof and explosion-proof, ship manufacturing, transportation facilities, vehicle manufacturing, building decoration, civil composite panels, and other fields.
Can produce and customize aluminum honeycomb,aluminum sponge, and aluminum covered foam panels of different specifications and sizes.
What is Aluminium Foam?
Aluminum metal foam, also known as the aluminum foam panel, is made by adding additives to pure aluminum or aluminum alloy through a foaming process. Simply put, it is a metal plate with N holes
According to the different control of foamed aluminum in the production process, there will be surface styles such as single-sided open cell, double-sided open cell, and closed-cell.
At the same time, foamed aluminum can also have a variety of colors. In addition to the true color of aluminum, like other aluminum plates, the color of foamed aluminum can be rendered colorful through metal treatment processes such as spraying.
Thanks to the special production process, there are more styles of foamed aluminum and a wider range of applications. It can be used to cover exterior walls, interior walls, ceilings, floors, and stairs required for architectural decoration. area.
Physical Characteristics of Huaxiao Aluminum Foam* (8% Nominal Density 6101-T6)
Compression Strength | 367 psi | (2.53 MPa) |
Tensile Strength* | 180 psi | (1.24 MPa) |
Shear Strength* | 190 psi | (1.31 MPa) |
Modulus of Elasticity (Compression)* | 15 × 103 psi | (103.08 MPa) |
Modulus of Elasticity (Tension)* | 14.6 × 103 psi | (101.84 MPa) |
Shear Modulus | 2.9 × 104 psi | (199.95 MPa) |
Vickers Pyramid Number | 35 HV | |
Specific Heat | .214 BTU/lb-°F | (.895 J/g-C) |
Bulk Thermal Conductivity | 3.4 BTU/ft-hr-F | (5.8 W/m-C) |
Coefficient of Thermal Expansion (0-100°C) | 13.1 × 10-6 in/in–F | (23.58 × 10-6 m/m–C) |
Bulk Resistivity | 2.84 × 10-5 ohm – in | (7.2 × 10-5 ohm – cm) |
Melting Point | 1220°F | (660°C) |
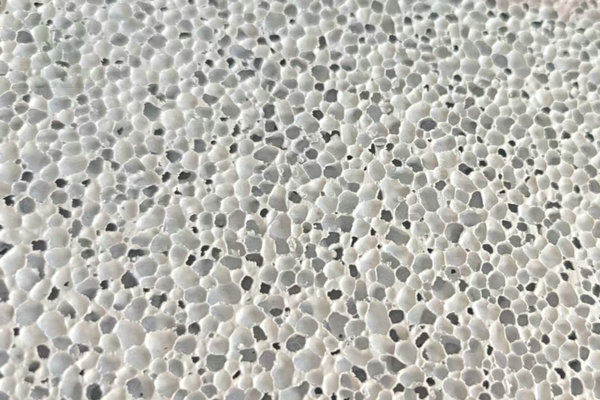
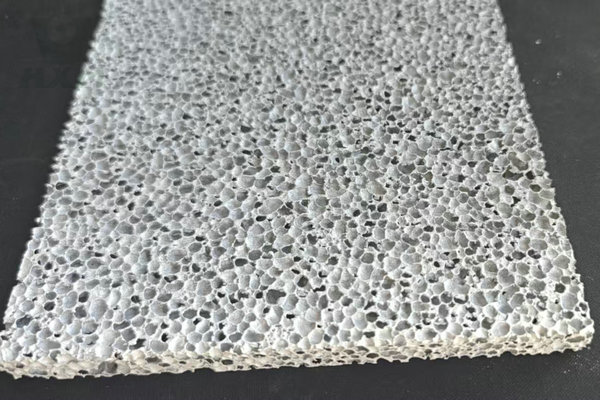
Performance Characteristics of Aluminum Metal Foam
Lightweight, strong and environmentally friendly
The aluminum foam density is about 1/5~1/10 of pure aluminum, 1/20 of iron, and 1/4 of wood and plastic. Its bending stiffness is 1.5 times that of steel. The unique lightweight panel is very suitable as a building skin, and the aluminum foam panels are completely recycled, which is very environmentally friendly.
Before being used in the field of architectural decoration, foamed aluminum began to be used in the field of automobile manufacturing, which can reduce the weight of vehicles and improve fuel efficiency.
Strong weather resistance, non-hygroscopic, heat-resistant/non-combustible characteristics
Thanks to the strong weather resistance of foamed aluminum, the cost-effectiveness of aluminum foam is still very high in terms of building life and service life, as well as maintenance costs.
According to relevant laboratory data, aluminum foam has been exposed to the ocean atmosphere for one year without any obvious abnormality. The surface can be sprayed with anti-corrosion treatment to further improve the anti-corrosion ability
The aluminum metal foam has a moisture absorption rate of 0.0%, no moisture absorption, and will not reduce the acoustic performance due to moisture.
Tested by the National Fireproof Building Material Quality Supervision and Inspection Center, the combustion performance has reached A1 level. At the same time, the linear expansion coefficient of foamed aluminum is 19.34*107°C, which is equivalent to concrete and is not easily deformed when heated.
Heat insulation, noise reduction, electromagnetic shielding
As a foam material, foamed aluminum has excellent thermal insulation effect. The insulation effect of closed-cell aluminum foam is equivalent to that of marble, and the weight is less than half of marble.
At the same time, it has a good acoustic function. The sound insulation coefficient of closed-cell aluminum foam is above 0.9. The sound absorption coefficient of through-hole aluminum foam can reach 0.8.
For office buildings, a space with more cluttered signals can have a good electromagnetic shielding effect. When the electromagnetic wave frequency is between 2.6-18GHZ, the electromagnetic shielding ability of foamed aluminum can reach 60-90dB.
Aluminum Foam Applications
Aluminum foam is a new type of light metal material produced by using bionic structure principles and using aluminum alloy foam. It is light and strong, has low density, high specific strength, and has sound insulation and noise reduction, electromagnetic shielding, energy absorption buffering, and resistance. Many excellent properties such as combustion and explosion protection are widely used in aerospace, equipment manufacturing, transportation facilities, building decoration, civil panels and other fields.
How to Make Aluminum Foam?
Aluminum foam is a lightweight, porous material that has many useful properties, such as high strength-to-weight ratio and good thermal and acoustic insulation. Here is a general process for making aluminum foam:
Preparing the aluminum: The first step is to melt the aluminum using a furnace or other heating method. Once the aluminum is melted, any impurities or gases must be removed to ensure a high-quality foam.
Adding a foaming agent: A foaming agent is added to the molten aluminum to create gas bubbles within the liquid metal. There are several different types of foaming agents that can be used, including titanium hydride, calcium carbonate, and aluminum powder.
Casting the foam: The foamed aluminum is then poured into a mold or shaped using other methods, such as extrusion or injection molding. The foam can be made in a variety of shapes and sizes, depending on the application.
Cooling and solidification: Once the foam is cast, it must be allowed to cool and solidify. The cooling process can be controlled to achieve a desired level of porosity and density.
Finishing: The foam may require some finishing, such as trimming or sanding, to achieve the desired shape and surface finish.
Overall, the process for making aluminum foam can be complex and requires specialized equipment and expertise. However, the resulting material can be extremely useful for a wide range of applications.
Why Choose Huaxiao Metal as Your Aluminum Foam Supplier?
At Huaxiao Metal, we provide high-quality aluminum foam panels and tubes that meet international standards. Here are the reasons why customers choose us:
Trustworthy Aluminum Foam Manufacturer: With years of expertise, we produce high-performance aluminum foam metal for various needs.
Wide Product Range: From panels to custom shapes, we offer aluminum metal foam in various sizes and densities.
Competitive Aluminum Foam Prices: Our efficient production ensures a cost-effective solution.
Global Shipping: Fast delivery, ensuring you receive your materials on time.
Looking for quality aluminum foam panels or custom aluminum metal foam products? Contact us today to discuss your project requirements.
Contact Shanghai Huaxiao's Aluminium Foam Manufacturers Now
