What is Mold Steel?
Mold steel refers to a specialized type of steel designed for use in making molds and tooling for industrial processes such as injection molding, die casting, and extrusion.
What is Carbon Steel?
Carbon steel is a versatile and widely used category of steel that primarily consists of iron and carbon, with small amounts of other alloying elements such as manganese, silicon, and sometimes chromium.
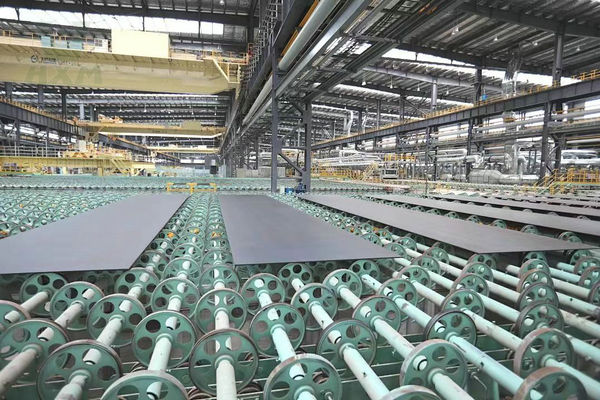
Which Hardness of Mold Steel and Carbon Steel Is High?
The hardness of mold steel is generally higher than that of carbon steel, which can reach 50-6HRC or more. Compared with carbon steel, mold steel has a higher carbon content and a denser structure, so its hardness is higher. The hardness of carbon steel is a type of steel with a high carbon content, which is characterized by high strength and good wear resistance.
Stainless steel is also one of the commonly used metal materials, but there is also a gap in hardness compared with H13 mold steel plate. Generally, the hardness of stainless steel is between 30~4HRC. Although stainless steel has excellent corrosion resistance and aesthetics, its low hardness limits its application range in high-load and high-friction environments.
C45W steel is a medium-carbon steel with low price and convenient processing. It is suitable for surface hardening treatments such as high-frequency induction heating quenching and flame quenching.
The hardness of tempered steel is generally 38~42HRC. Tempered steel generally refers to medium-carbon steel with a carbon content of 3~6%. Generally, parts using this type of steel are required to have good comprehensive mechanical properties, that is, good plasticity and toughness while maintaining high strength.
Carbon die steel has high strength and hardness and is suitable for cutting tools and tool steel. Low-carbon die steel is mainly divided into four stages on the tensile stress-strain curve: elastic stage, yield stage, strengthening stage, and local deformation stage. There are obvious yield and necking phenomena in the local deformation stage.
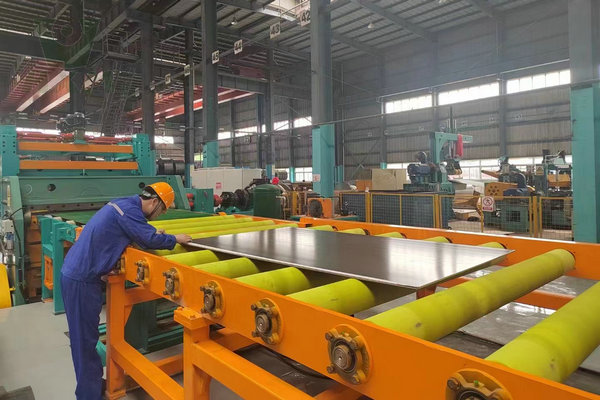
Hardness of high carbon steel: its hardness is between 65-7HRC.
The hardness of alloy structural steel: hardness of low alloy steel: its hardness is between 50-6HRC.
The hardness of medium alloy steel: its hardness is between 60-6HRC.
The hardness of high alloy steel: its hardness is between 65-8HRC.
What Is the Difference Between Mold Steel and Other Steel?
Property | Mold Steel | Carbon Steel |
---|---|---|
Composition | Contains alloying elements (e.g., chromium, nickel, molybdenum) to enhance properties like hardness, wear resistance, and toughness. | Primarily iron and carbon, with other alloying elements in smaller quantities (e.g., manganese, silicon). |
Hardness | Typically higher hardness to withstand repeated impacts and wear. | Generally lower hardness compared to mold steel. |
Strength | Higher strength, especially in hardened and tempered conditions. | Moderate to high strength depending on the alloy composition and heat treatment. |
Wear Resistance | Excellent wear resistance, crucial for prolonged use in molding processes. | Moderate wear resistance; may require coatings or treatments for improved durability. |
Toughness | Good toughness to resist cracking and deformation under high-stress conditions. | Generally good toughness; less prone to brittleness compared to hardened mold steels. |
Corrosion Resistance | Varies; some grades offer good corrosion resistance, and others may require coatings. | Moderate corrosion resistance; susceptible to rust and oxidation without proper protection. |
Machinability | Typically more challenging to machine due to hardness and alloy content. | Generally easier to machine compared to mold steel. |
Heat Resistance | High heat resistance, retaining hardness and strength at elevated temperatures. | Limited heat resistance; can soften or deform at high temperatures. |
Applications | Injection molds, die-casting molds, extrusion dies, and other tooling applications require high wear resistance and dimensional stability. | Structural components, machine parts, shafts, and general-purpose tools where wear resistance and strength are necessary. |
Mold steel has good wear resistance and small deformation during heat treatment. It is used to make cold stamping mold steel with high hardness, does not easily break corners or missing corners, and has a long service life. It is used to make injection mold steel with good polishing performance and is easier to achieve a mirror effect.
Mold steel is a type of steel used to make cold stamping dies, hot forging dies, die-casting dies, and other molds. It is the main material for making molds. Molds are the cornerstone of industry, and almost all manufacturing industries are direct and indirect users of molds.
Mold steel is a special high-quality steel because the hardness, wear resistance, corrosion resistance and other characteristics of this steel will change with factors such as temperature and salinity. It is used to make cold stamping dies, hot forging dies, die-casting dies and other molds.
Commonly used hot working die steels include: alloy die steels with high carbon content and added alloy elements such as Cr, W, Mo, and V; for hot working die steels with special requirements, high-alloy austenitic heat-resistant die steel is sometimes used.
Due to the special requirements of mold steel, the production process of this type of steel requires refined materials, refining and vacuum degassing. The carbon content range in the steel is narrowed to control the lower sulfur and phosphorus content. For example, in YB/T107-1997, the steel grades of carbon plastic mold steel are defined as SM4, SM4SM5, SM53 and SM55, etc., to distinguish them from high-quality carbon structural steels for general purposes.