In the field of Knife Making Steel, the choice of steel determines the performance, durability and user experience of the knife. Different types of knife steel have their own characteristics in terms of hardness, toughness, corrosion resistance and wear resistance, and are suitable for different application scenarios. Whether it is a kitchen knife, outdoor knife or industrial cutting tool, choosing the right knife steel can not only increase the service life of the knife, but also affect its maintenance cost and user experience.
This article will explore the key performance of knife steel, common material types and the differences between different steels, and answer common knife steel questions to help you choose the most suitable knife steel. If you have any needs for purchasing or customizing knife steel, please contact us for the latest knife steel quotation.
What is Knife Making Steel?
Knife steel refers to high-performance alloy steel used to make knives. Its core feature is the ability to maintain a sharp edge while having sufficient strength and wear resistance to adapt to various cutting needs. Knife steel is usually optimized through heat treatment processes (such as quenching, tempering, etc.) to optimize its mechanical properties to ensure the durability and sharpness of the knife.
Knife steel is widely used in kitchen utensils, hunting knives, tactical knives, industrial cutting tools, and medical scalpels. Different applications have different performance requirements for knife steel. For example, kitchen knives focus more on corrosion resistance, while outdoor knives emphasize toughness and wear resistance.
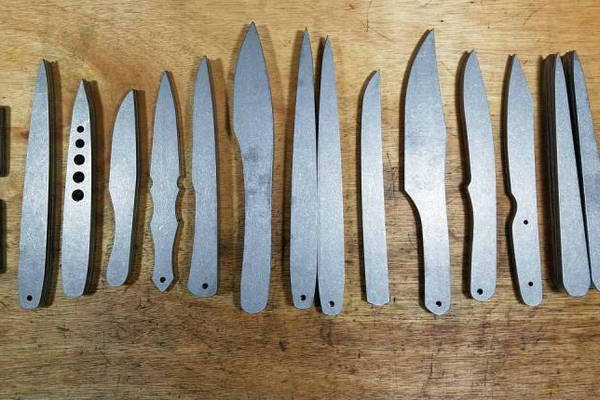
Key Properties of Knife Steel
The properties of knife steel determine the lifespan and application range of knives. Here are some key factors to consider when choosing knife steel:
Hardness
Hardness is a measure of the ability of knife steel to resist deformation and edge curling, usually expressed in Rockwell hardness (HRC). Knife steels with high hardness can maintain a sharp edge, but they are often less tough and more prone to breaking. For example, D2 steel and M390 steel have high hardness and are suitable for making high-end knives.
Toughness
Toughness refers to the ability of knife steel to resist impact and breakage. Highly tough steel can effectively prevent blade chipping, especially for heavy-duty cutting tasks. Carbon steel is generally tougher than stainless steel. For example, 5160 spring steel is widely used to make machetes and tactical knives.
Corrosion Resistance
Corrosion resistance determines whether a knife is prone to rust, especially in wet environments or food processing applications. Stainless steels (such as 440C and VG10) have excellent oxidation resistance due to their high chromium content, which is suitable for kitchen knives and outdoor knives.
Wear Resistance
Wear resistance affects the durability of a knife edge and how quickly it wears. Steels with high wear resistance will remain sharp after long periods of use. For example, M390 and CPM-S90V are extremely wear-resistant due to their high proportions of vanadium and carbon.
Edge Retention
Edge retention refers to the ability of a knife to remain sharp after use. Steels with high hardness and good wear resistance generally retain their sharpness longer. Steels such as S30V and S35VN are common choices for high-end knives.
knife Steel Types
Different types of knife steel have their advantages, and the common classifications are as follows:
Stainless Steel
Stainless steel contains at least 10.5% chromium and has good corrosion resistance. It is suitable for humid environments and food processing applications. Common stainless steel knife materials include:
- 420, 440C (cost-effective, suitable for the mass market)
- VG10, M390 (high-end knife steel, sharp and corrosion-resistant)
Carbon Steel
Carbon steel knives are favored by professionals for their high hardness and sharpness, but they are prone to rust and require regular maintenance. Common carbon steels include:
- 1095 (high hardness, suitable for tactical knives)
- O1 (high toughness, suitable for hand-forged knives)
Other Steels
In addition to stainless steel and carbon steel, there are some special steels used to make knives, such as:
- D2 steel (semi-stainless steel, high wear resistance)
- M390 (high-end powder metallurgy steel, wear-resistant and corrosion-resistant)
Differences Between Knife Steel Materials
Different knife steels have their own advantages and disadvantages in terms of hardness, toughness, corrosion resistance, etc. When choosing knife steel, you need to make a trade-off based on the specific use. For example:
Kitchen knives: Suitable for high corrosion-resistant steels such as 440C and VG10.
Outdoor survival knives: 1095 carbon steel and D2 steel are more suitable, with both hardness and toughness.
High-end collector knives: M390 and S30V provide excellent edge retention.
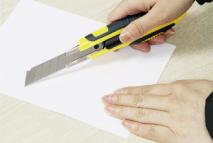
Knife Making Steel: FAQ
How to judge whether steel is suitable for making knives?
Steel suitable for making knives should have good hardness, toughness, wear resistance and corrosion resistance. The specific selection needs to be weighed according to the purpose.
Is 1018 steel suitable for making knives?
Not suitable, 1018 steel is a low-carbon steel with insufficient hardness and wear resistance to maintain a sharp blade.
Is 1095 steel good for knife making?
Yes, 1095 carbon steel has high hardness and good sharpness, but poor corrosion resistance and requires regular maintenance.
Is 304 steel suitable for making knives?
Not suitable, 304 stainless steel is mainly used in industry and kitchenware, and has a low hardness and cannot effectively maintain the edge of the knife.
Is 316 steel suitable for making knives?
Not suitable, 316 stainless steel has good corrosion resistance, but insufficient hardness and wear resistance, and is not suitable for making blades.
Is 420 steel suitable for making knives?
Yes, 420 steel has moderate hardness and good corrosion resistance, which is suitable for cheap knives and daily use knives.
Is 440 steel suitable for making knives?
Yes, especially 440C, which has high hardness, wear resistance and good corrosion resistance, suitable for high-end knives.
Is cold rolled steel suitable for knives?
It depends on the specific grade. Ordinary cold rolled steel has a low hardness and is not suitable for blades, but some high carbon cold rolled steels can be used for knife manufacturing.
Is hot rolled steel suitable for knives?
Usually not, hot rolled steel has a loose internal structure and needs further heat treatment to reach knife standards.
Is leaf spring steel suitable for knives?
Yes, such as 5160 leaf spring steel, which has good toughness and impact resistance, suitable for making machetes and Damascus knives.
Is rebar suitable for knives?
No, rebar is usually low carbon steel with low hardness and cannot maintain a sharp edge.
How to clean a carbon steel knife?
Use warm water, mild detergent and a soft cloth to clean, wipe dry and apply anti-rust oil for storage.
Is M390 a good knife steel?
Yes, M390 is a top-grade powder metallurgy stainless steel with excellent wear resistance and edge retention, suitable for high-end knives.
How to remove rust from carbon steel knives?
You can gently wipe it with white vinegar, citric acid or metal polishing paste, and then apply anti-rust oil to prevent rust.
Is D2 steel suitable for making knives?
Yes, D2 is a high-carbon, high-chromium semi-stainless steel with excellent wear resistance, but average toughness and easy to break.
Is 8Cr13MoV a good knife steel?
Yes, 8Cr13MoV has similar performance to 440C, high cost performance, and is suitable for mid-range knives.
Is VG10 a good knife steel?
Yes, VG10 has high hardness and strong corrosion resistance, suitable for high-end kitchen knives and folding knives.
In Conclusion: Knife Making Steel
Choosing the right knife steel is crucial. Stainless steel is suitable for corrosion resistance, while carbon steel provides better sharpness and toughness. For professional users and collectors, powder metallurgy steel (such as M390, S30V) is the best choice.
If you need to purchase high-quality knife steel, please contact us for a quote and more product information!