What is 3Cr13 Steel?
3Cr13 steel tube processing performance is good, after heat treatment (quenching and tempering), has excellent corrosion resistance polishing performance higher strength and wear resistance, suitable for manufacturing to withstand high loads, high abrasion resistance, and under the action of corrosive media plastic molds.
3Cr13 steel than 410 (1Cr13) and 420J1 (2Cr13) but also higher strength, hardness, and hardenability, at room temperature (700 degrees) of dilute HNO3 and weak organic acids have corrosion resistance, and weldability less than 410 and 410J1.
3Cr13 has a higher carbon content of martensitic stainless steel, compared with 1Cr13 and 2Cr13 steel has higher strength, hardness, and better hardenability.
3Cr13 steel machinability is good, after heat treatment (quenching and tempering), has excellent corrosion resistance polished performance of high strength and wear resistance, suitable for manufacturing to withstand high loads, high abrasion resistance, and under the action of corrosive media plastic molds. Tempering treatment after the hardness of HRC30 below 3Cr13 material processability is better, easy to achieve a better surface quality.
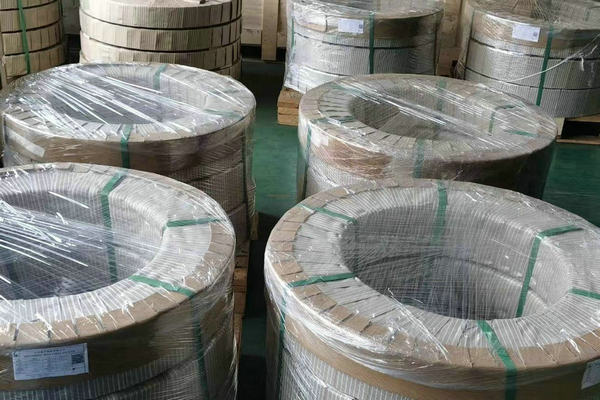
The hardness is greater than HRC30 when the parts are processed, and although the surface quality is better, the tool is easy to wear. Therefore, after the material into the factory, the first tempering treatment hardness to HRC25 ~ 30, and then cutting.
However, the corrosion resistance and thermal stability of this steel below 700°C are not as good as 1Cr13 and 2Cr13. 3Cr13 is mainly used for high-strength parts, and wear parts that are subjected to high stress loads and under conditions of corrosive media in a room. It is also widely used in measuring instruments, yi pliers, and so on. This steel should not be welded.
What is 3Cr13 and What Grade is it Equivalent to by US Standards?
3Cr13 is a martensitic type of stainless steel; corresponding to US grade: 420B.
3Cr13 belongs to martensitic stainless steel, the executive standard: GB/T 1220-2007
Chemical Composition of 3Cr13 Steel
Element | Content |
---|---|
C | 0.26 – 0.35% |
Si | ≤ 1.00% |
Mn | ≤ 1.00% |
P | ≤ 0.035% |
S | ≤ 0.030% |
Cr | 12.00 – 14.00% |
Ni | ≤ 0.60% |
3Cr13 Process Performance
Hot Working?
3Cr13 steel hot working temperature range of 850 ~ 1200 ℃, the appropriate hot working heating temperature of 1160 ~ 1200 ℃, before 850 ℃ should be slowly heated, cold loading furnace temperature should be less than 800 ℃. After hot working slow cooling or timely annealing.
Cold Working?
3Cr13 steel cold workability is poor, not recommended for cold working operations, but 3Cr13 steel can produce cold drawn steel, cold rolled sheet and wire.
3Cr13 Corresponding Grades
1, the national standard GB-T standard: digital grade: S42030, the new grade: 30Cr13, the old grade: 3Cr13,
2, the American standard: ASTMA standard: S42080, SAE standard: a, UNS standard: 420,
3, the Japanese standard JIS standard: sus420J2,
4, the German standard DIN standard: 1.4028,
5, the European standard EN standard: X30Cr13, French standard NF standard: z33c13.
3Cr13 Physical Properties
①Density Density (20 ℃) / kg / dm3: 7.76,
②Melting point/°C:1365,
③Specific heat capacity (0~100℃)/kg/(kg.k):0.17,
④ Thermal conductivity/w/(m.k)100℃-:25.1,
⑤ Thermal conductivity/w/(m.k)500℃-:25.5,
⑥ Coefficient of linear expansion/(10-6/k)0~100℃:10.5,
⑦Coefficient of linear expansion/(10-6/k)0~594℃:12,
⑧ Resistivity (20℃)/(.mm2/m):0.52,
⑨Longitudinal modulus of elasticity(20℃)/GPa:219,.
⑩Magnetic:Yes
3Cr13 Mechanical Properties
(1) delivery status: bar solution treatment, plate solution pickling, (2) tensile strength (RM / MPa): 735, 540, (3) elongation strength (Rp0.2 / MPa): 540, 225, (4) elongation A/%: 18, (5) section shrinkage (Z / %): 40.
3Cr13 heat treatment: ① hardness HBW ≤: annealed 235, quenched and tempered 217, hardness HRB ≤: 99, ② heating temperature: 800 ~ 900, ③ heating mode: air cooling or slow cooling.
3Cr13 application areas: mainly used for high-strength parts and bear high strength pressure load and wear parts under the condition of corrosive media, such as cutting tools and springs working below 300 degrees, and working shafts below 400 degrees. Bolts, valves, bearings, et
Characteristics
The carbon content of 3Cr13 steel is less than 0.35, the hardness obtained after heat treatment is only HRc52-55, and the resistance to damage and other aspects of the performance are not too outstanding. Because it is easier to cut and polish, it is suitable for mass production of factory-made knives, 420 steel is also due to the low carbon content and excellent rust resistance, so it is also the production of cutting tools of the ideal steel.
3Cr13 stainless steel has a certain degree of abrasion resistance corrosion resistance, and high hardness, the price of its stainless steel ball is the lower class, suitable for stainless steel common requirements of the working environment.
Apply to all kinds of precision machinery, bearings, electrical, equipment, instruments, meters, transportation tools, household appliances, and so on. Mostly used in the manufacture of parts resistant to atmospheric, water vapor, water, and oxidizing acid corrosion.2Cr13 stainless steel: high hardness after quenching, good corrosion resistance (magnetic) 3Cr13 stainless steel quenched, then the hardness of 2Cr13 steel rises (magnetic).
3Cr13 steel is martensitic stainless steel used after quenching and tempering. Relative to 1Cr13, 2Cr13 steel has higher strength, hardness, and hardenability, but its corrosion resistance and thermal stability below 700 ℃ is lower than 1Cr13, 2Cr13 steel. Cold working properties and welding performance are not good, heat treatment should be done immediately after welding to prevent Cracking. In the annealed state has good cutting performance.
Mechanical Properties
Tensile strength (MPa): quenched and tempered, ≥735
Conditional yield strength 0.2 (MPa): quenched and tempered, ≥540
Elongation:quenched and tempered,≥12%.
Section shrinkage? (%): quenched and tempered, ≥40
Impact work Akv (J): quenched and tempered,≥24
Hardness Annealed,≤235HB;quenched and tempered,≥217HB
Density 7.75g/cm3
Heat Treatment
Bar and forging: 1000~1050℃ oil quenching or air cooling, 200~300℃ tempering. Plate: annealed at 740~780℃ or tempered at high temperature.
Melting and casting process: can be smelted by electric arc furnace, electric arc furnace + electroslag remelting and other methods.