Aluminum metal alloys., a versatile metal widely used in various industries, come in different alloys with distinct properties. Two prominent alloys, 7075 and 2024, are often compared for their specific characteristics. Understanding the differences between 7075 aluminum vs 2024 aluminum is crucial for making informed decisions in aerospace and manufacturing applications.
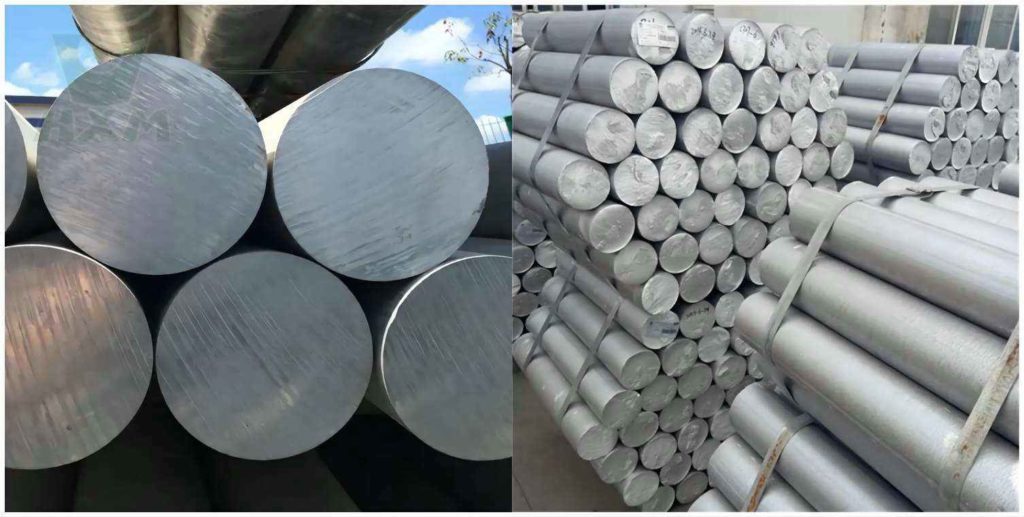
What is 2024 Aluminum Alloy?
2024 aluminum alloy is a high-strength, heat-treatable aluminum alloy primarily composed of copper as the major alloying element, along with smaller amounts of manganese, magnesium, and traces of other elements. This alloy belongs to the 2000 series of aluminum alloys and is known for its excellent strength-to-weight ratio, good machinability, and high fatigue resistance.
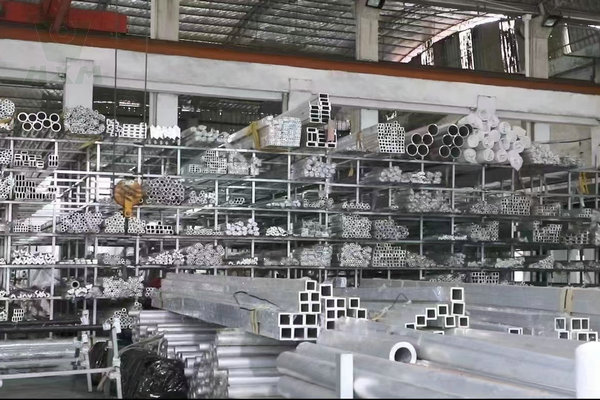
What is 7075 Aluminum Alloy?
7075 aluminum alloy is a high-strength, heat-treatable aluminum alloy known for its excellent strength-to-weight ratio and good mechanical properties. It belongs to the 7xxx series of aluminum alloys, which are aluminum-zinc-magnesium alloys. The primary alloying elements in 7075 are aluminum, zinc, and copper.
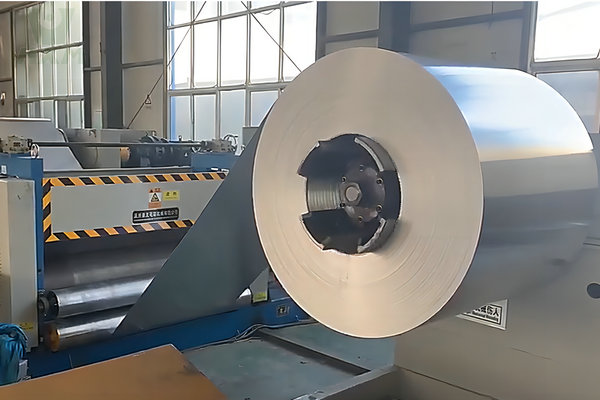
The Difference Between 7075 Aluminum vs 2024 Aluminum
Composition and Alloying Elements:
The first key aspect to consider is the composition of these alloys. Both 7075 and 2024 belong to the aluminum-zinc-magnesium family, but their specific alloying elements set them apart. 7075 contains a higher percentage of zinc and copper, contributing to its superior strength. On the other hand, 2024 has a significant amount of copper, which enhances its machinability.
Element | 2024 Aluminum Alloy | 7075 Aluminum Alloy |
Cu | 3.8-4.9 | 1.2-2 |
Fe | 0.5 | 0.5 |
Mn | 0.3-0.9 | 0.9 |
Mg | 1.2-1.8 | 2.1-2.9 |
Cr | 0.1 | 0.18-0.28 |
Si | 0.5 | 0.4 |
Zn | 0.25 | 5.1-6.1 |
Ti | 0.15 | 0.2 |
Mechanical Properties: 7075 Aluminum vs 2024 Aluminum
Property | 7075 Aluminum | 2024 Aluminum |
---|---|---|
Tensile Strength (MPa) | 572–638 | 400–500 |
Yield Strength (MPa) | 503–572 | 275–310 |
Elongation (%) | 5–11 (depending on heat treatment) | 10–15 (depending on heat treatment) |
Hardness (HB) | 150–160 | 120–130 |
Density (g/cm³) | 2.81 | 2.78 |
Elastic Modulus (GPa) | 71.7 | 73.1 |
Fatigue Strength (MPa) | 159 | 138 |
Shear Strength (MPa) | 331–386 | 255–283 |
Corrosion Resistance | Excellent (with anodizing) | Poor (requires additional protection) |
Weldability | Poor (suitable for mechanical joints) | Poor (prone to hot cracking) |
Machinability | Excellent | Excellent |
Strength and Durability:
One of the primary differentiators between these two alloys is their strength. 7075 aluminum is renowned for its exceptional strength, making it one of the strongest aluminum alloys available. This strength is achieved through zinc and copper, making 7075 ideal for applications requiring high tensile strength. In contrast, 2024 offers good strength, but it falls short when compared to the impressive strength of 7075.
Machinability and Formability:
While 7075 aluminum boasts superior strength, it is less machinable than 2024. The higher levels of zinc and copper in 7075 contribute to its lower machinability, making it challenging to work within certain applications. Conversely, 2024, with its higher copper content, is more easily machined and exhibits better formability, making it a preferred choice in situations requiring intricate shapes.
Corrosion Resistance: 7075 Aluminum vs. 2024 Aluminum
7075 aluminum is more corrosion-resistant than 2024 aluminum, especially when anodized or coated.
2024 aluminum is very susceptible to corrosion, especially in wet or salty environments.
So for high humidity or corrosive environments, 7075 aluminum is a better choice.
2024 aluminum requires additional protection, so it is less cost-effective in highly corrosive conditions.
Welding Performance: 7075 Aluminum vs. 2024 Aluminum
Welding Performance of 2024 Aluminum
Features: The welding performance of 2024 aluminum is poor, especially for fusion welding (such as TIG and MIG welding). Due to its high copper content, thermal cracks are easily formed during welding.
Applicable situations: Welding is generally not recommended for connection. Mechanical connection (such as riveting or bolting) is usually used to avoid performance degradation.
Improvement method: In special cases, welding performance can be improved by reducing heat input or using suitable filler metal (such as 2319 aluminum alloy welding wire), but the ideal effect cannot be achieved.
Welding Performance of 7075 Aluminum
Features: The weldability of 7075 aluminum is also poor, but it is better than that of 2024 aluminum. This is mainly because the high aluminum-zinc content of 7075 makes it easy to form cracks during welding, and the strength of the heat-affected zone is significantly reduced.
Applicable situations: Welding will significantly affect the mechanical properties of the material, so it is more inclined to use mechanical processing or mechanical connection methods, such as bolting, riveting, etc.
Improvement method: The welding of 7075 aluminum is generally only used for non-critical components. The performance of the welding area can be improved by adding subsequent heat treatment, but the operation is complicated and costly.
Cost: 7075 Aluminum vs. 2024 Aluminum
7075 aluminum is usually more expensive than 2024 aluminum. Because 7075 aluminum has higher strength and better overall performance, especially in high-demand fields such as aerospace, its manufacturing cost and market demand make it more expensive. In addition, the surface treatment and processing costs of 7075 aluminum are also higher because it has poor weldability and is more difficult to process.
In contrast, 2024 aluminum is cheaper and is a more cost-effective alloy material. Although not as strong as 7075 aluminum, it excels in fatigue performance and easy processing and is suitable for applications with limited budgets but high performance.
In general, the choice of which aluminum alloy to choose is a balance between performance and cost based on specific needs. For accurate pricing information, please contact us for a quote!
Applications:
The differences in properties between 7075 and 2024 aluminum alloys make them suitable for distinct applications. 7075, with its superior strength, is often chosen for aerospace components, high-stress structural parts, and military applications where strength is paramount. On the other hand, 2024, with its better machinability, finds its place in applications like manufacturing, precision parts, and components where formability is crucial.
2024-T3 Aluminum vs. 7075-T6 Aluminum
2024-T3 aluminum and 7075-T6 aluminum are both high-strength aerospace-grade alloys, but they differ in several key ways:
- Strength: 7075-T6 has higher tensile and yield strengths than 2024-T3, making it better suited for heavy-duty applications.
- Fatigue resistance: 2024-T3 has excellent fatigue resistance, making it well-suited for cyclic loading.
- Corrosion resistance: 7075-T6 has better corrosion resistance, especially when anodized, while 2024-T3 is more susceptible to corrosion and typically requires a protective coating.
- Weldability: Both are poorly weldable, but 2024-T3 is easier to weld with specialized techniques.
Applications:
- 2024-T3: Aircraft skins, fuselage components, and applications requiring high fatigue resistance.
- 7075-T6: Aerospace frames, structural components, and highly stressed parts.
- For fatigue critical applications, choose 2024-T3; for projects requiring high strength, choose 7075-T6.
In Conclusion:
In the choice between 7075 aluminum vs 2024 aluminum, the decision ultimately depends on the specific requirements of the application. If unparalleled strength is the priority, 7075 is the clear choice. However, if machinability and formability are more critical factors, 2024 may be the preferred option. Understanding the differences in composition, strength, machinability, and corrosion resistance is essential to make informed decisions when selecting the right aluminum alloy for a particular use case.