What are the benefits of aluminum metal sheet slitting? Why do we need to know these benefits? That’s because the global aluminum market is expanding rapidly, with experts predicting it will grow from $175.85 billion in 2022 to $265.82 billion in 2030. As manufacturers and exporters of aluminum metal sheets, we need to fully use this period of rapid development and allow our company to occupy a larger share of the global market.
Aluminum metal is widely used in many industries including construction, transportation, and packaging due to its lightweight, corrosion-resistant properties and excellent formability. As sustainability becomes increasingly important, industries are looking for new applications for aluminum panels, with construction companies incorporating aluminum into their exterior building materials and car manufacturers seeing the potential of aluminum panels to lighten vehicles and improve vehicle fuel efficiency.
What Is Aluminum Metal Sheet Slitting?
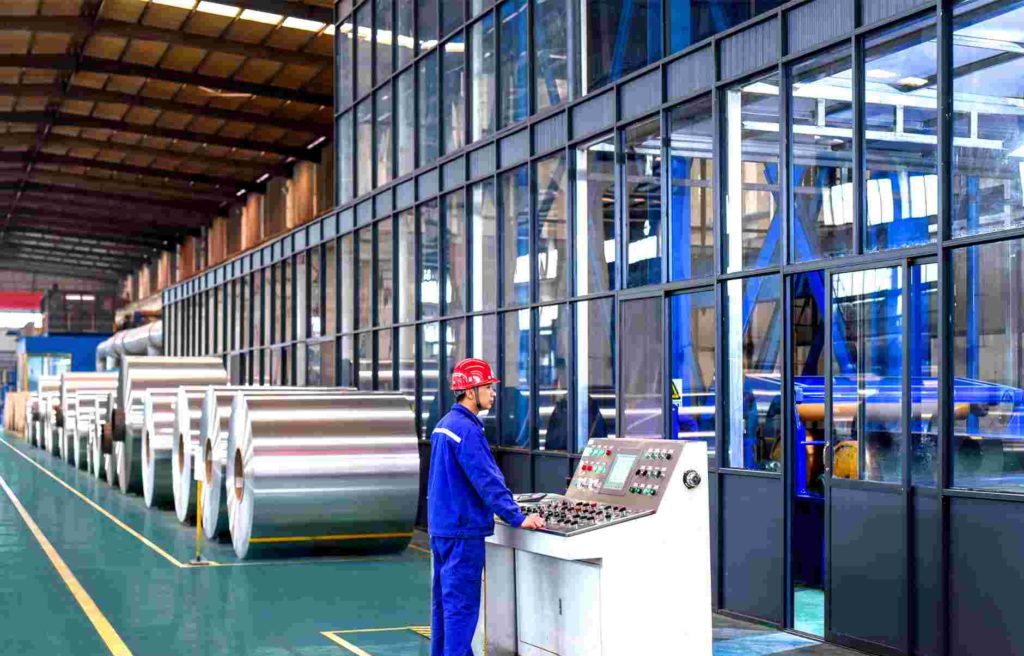
Aluminum metal sheet slitting is a manufacturing process used to cut large coils or rolls of aluminum into narrower strips or sheets. This process is commonly employed in industries where customized widths of aluminum are required for specific applications. The primary goal of slitting is to convert large, wide coils of aluminum into smaller, more manageable strips while maintaining precision and efficiency.
Here’s a step-by-step overview of the aluminum metal sheet slitting process:
- Coil Unloading:
Large coils of aluminum, typically obtained from aluminum rolling mills, are transported to the slitting facility.
- Coil Inspection:
The coils are inspected for any defects, and the quality of the material is assessed before proceeding with the slitting process.
- Loading onto Slitting Machine:
The coil is loaded onto a slitting machine, which is equipped with sharp circular blades and other components necessary for the slitting operation.
- Guiding and Tensioning:
The coil is guided through the slitting machine, and tension is applied to ensure the material remains stable during the cutting process.
- Slitting Operation:
The aluminum coil passes through the slitting machine, where circular blades make precise cuts along the length of the coil, dividing it into narrower strips. The number of blades and their positioning determine the width of the resulting strips.
- Separation and Recoiling:
The slitted aluminum strips are separated and wound onto individual recoiler drums. This process may involve several recoiling stations, allowing for different widths to be produced simultaneously.
- Quality Control:
Throughout the slitting process, various quality control measures are implemented to ensure that the resulting aluminum strips meet the specified requirements in terms of width, thickness, and overall quality.
- Packaging and Shipping:
The final slitted aluminum sheets are typically packaged and prepared for shipment to customers or further processing. Packaging methods may vary depending on the application and customer specifications.
Aluminum sheet slitting offers flexibility and customization, allowing manufacturers to produce aluminum strips with specific widths tailored to their requirements. This process is widely used in industries such as automotive, construction, packaging, electronics, and more, where aluminum in various dimensions is needed for specific applications.
Advantages of Aluminum Metal Sheet Slitting
Aluminum metal sheet slitting, a process that involves cutting large coils of aluminum into narrower strips, offers several advantages in various industries. Here are some of the key advantages:
Customization and Precision:
- Aluminum sheet slitting allows for precise customization of the width of the strips, meeting specific size requirements for different applications. This precision is crucial in industries where tight tolerances are essential.
Cost Efficiency:
- Slitting helps optimize material usage by minimizing waste. It allows manufacturers to produce the exact width required for their products, reducing the need for excess material and ultimately cutting costs.
Increased Productivity:
- Slitting machines are capable of high-speed processing, contributing to increased overall productivity. This is particularly important in industries with high-volume production requirements.
Flexibility in Production:
- Aluminum sheet slitting provides flexibility in terms of the width and thickness of the final product. Manufacturers can adjust the slitting process to accommodate different specifications and production needs.
Enhanced Material Handling:
- Narrower strips resulting from the slitting process are easier to handle, transport, and store. This can simplify logistics and contribute to a more efficient supply chain.
Reduced Lead Times:
- The ability to quickly produce custom-width aluminum strips means reduced lead times for manufacturers. This is crucial in industries where rapid response to market demands is necessary.
Improved Quality Control:
- Slitting machines are equipped with advanced technologies for quality control, ensuring consistent strip width and minimizing variations. This leads to higher-quality end products.
Versatility in Applications:
- Slitted aluminum sheets find applications in a wide range of industries, including automotive, construction, packaging, and electronics. The versatility of the process makes it suitable for various end-use products.
Material Savings:
- Aluminum sheet slitting allows for efficient use of raw materials, as manufacturers can obtain the desired widths with minimal waste. This is especially important in industries where materials can be costly.
Adaptability to Market Trends:
- The ability to quickly adjust production to changing market demands makes aluminum sheet slitting a valuable process for manufacturers looking to stay competitive in dynamic markets.
In summary, aluminum sheet slitting offers a combination of precision, cost efficiency, productivity, and adaptability, making it a favored method for processing aluminum coils in diverse industrial applications.