Aluminum alloys are widely used materials in modern manufacturing and construction. Its lightweight, high strength and good corrosion resistance make it one of the first choices in many applications. Among many aluminum 6061 vs 6063 materials have attracted much attention due to their unique performance characteristics.
Although they are numerically very similar they have some significant differences in their uses, processing characteristics, and mechanical properties. This article will take an in-depth look at these two aluminum alloys and discuss their respective characteristics and differences in practical applications to help readers better understand when to choose 6061 or 6063 materials.
What is 6061 Aluminum Alloy?
6061 aluminum alloy is a widely used heat-treatable aluminum alloy with a combination of excellent mechanical properties, good weldability, and high corrosion resistance. It belongs to the 6xxx series of aluminum alloys, which are aluminum-magnesium-silicon alloys. The primary alloying elements in 6061 are aluminum, silicon, and magnesium.
What is 6063 Aluminum Alloy?
Compared with 6061, 6063 aluminum alloy contains more silicon in its composition, which makes it excellent in corrosion resistance and processability. Due to its good surface treatment properties, 6063 is commonly used in construction and decorative applications such as window and door frames, aluminum alloy pipes, etc.
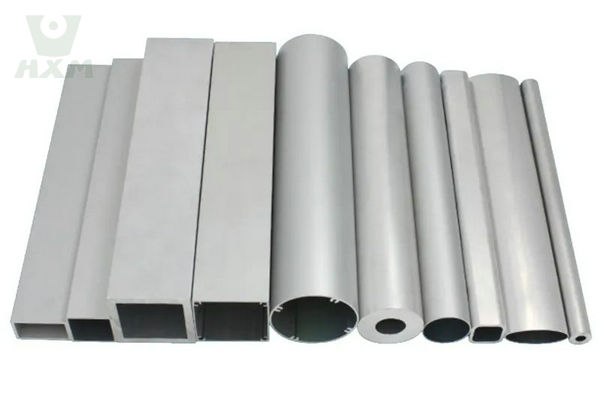
6063 Aluminum Alloy
6063 Aluminum Alloy Suppliers | Manufacturer | Factory Welcome to Huaxiao Metal Company, you deserve the best quality 6063 aluminum alloy products! Aluminum alloy 6063
The Difference Between Aluminum 6061 vs 6063 Aluminum
Let’s compare aluminum 6061 vs6063 from different perspectives, including composition, mechanical properties, cost, application, etc.
Chemical Composition of Aluminum 6061 vs 6063:
Element | 6061 (%) | 6063 (%) |
---|---|---|
Al | 97.9 | 98.9 |
Si | 0.6-1.0 | 0.2-0.6 |
Mg | 1.0-1.4 | 0.45-0.9 |
Cu | 0.15-0.4 | 0.1 |
Mn | 0.15 | 0.1-0.6 |
Cr | 0.04-0.35 | 0.1 |
Zn | 0.25 | 0.1 |
Ti | 0.15 | – |
Fe | 0.7 | 0.35 |
Mechanical Properties of Aluminum 6061 vs 6063:
Here is a table presenting the mechanical properties of Aluminum 6061 and 6063:
Property | 6061 Alloy | 6063 Alloy |
---|---|---|
Tensile Strength (MPa) | 310 | 185 |
Yield Strength (MPa) | 276 | 145 |
Elongation at Break (%) | 12 | 12 |
Hardness (Brinell, HB) | 95 | 73 |
Shear Strength (MPa) | 207 | 124 |
Modulus of Elasticity (GPa) | 68.9 | 68.3 |
Poisson’s Ratio | 0.33 | 0.33 |
Characteristics of Aluminum 6063 vs 6061:
Aluminum 6061 Characteristics:
Strength and Hardness: 6061 aluminum alloy is known for its high strength and hardness, making it suitable for applications requiring structural integrity and load-bearing capacity.
Weldability: 6061 offers good weldability, allowing for ease of fabrication and assembly in various industries.
Corrosion Resistance: While not as corrosion-resistant as some other aluminum alloys, 6061 exhibits reasonable corrosion resistance, especially when compared to certain other metals.
Machinability: The alloy has good machinability, making it suitable for precision machining processes such as milling, drilling, and turning.
Heat Treatment: 6061 is a heat-treatable alloy, commonly used in the T6 temper for achieving the highest mechanical properties.
Common Applications: Aerospace components, automotive parts, bicycle frames, structural components, and high-stress applications benefit from the strength and toughness of 6061 aluminum.
Aluminum 6063 Characteristics:
Extrudability: 6063 is highly known for its excellent extrudability, making it a preferred choice for applications that involve complex shapes and profiles, particularly in architectural and structural designs.
Surface Finish: This alloy provides a superior surface finish, making it suitable for visible applications like window frames, door frames, and other decorative elements.
Corrosion Resistance: 6063 exhibits good corrosion resistance, particularly in comparison to other alloys with similar extrusion characteristics.
Weldability: It has good weldability, allowing for the creation of strong joints without compromising the integrity of the material.
Heat Treatment: While 6063 is not as heat-treatable as 6061, it can still be subjected to heat treatment processes to enhance certain properties.
Common Applications: Architectural extrusions, window and door frames, heat sinks, and other applications where a combination of formability and corrosion resistance is crucial.
Differences:
Strength: 6061 is generally stronger than 6063, making it preferred for applications requiring higher strength and load-bearing capacity.
Extrudability: 6063 excels in extrudability, making it ideal for applications that demand intricate shapes and designs.
Common Applications: 6061 is commonly found in high-stress applications, while 6063 is often chosen for its aesthetic appeal in architectural and decorative applications.
Cost of Aluminum 6061 vs 6063:
The cost of aluminum 6061 vs 6063, can vary based on several factors such as market conditions, availability of raw materials, processing methods, and the specific supplier. Generally, both 6061 and 6063 aluminum alloys are competitively priced, but there can be some differences in cost. Here are a few factors that might influence the cost of each alloy:
Composition and Raw Materials:
- The cost of the raw materials used in the alloy composition can impact the overall cost. Elements like magnesium and silicon, which are present in different amounts in 6061 and 6063, can have varying costs.
Processing and Manufacturing:
- The manufacturing processes, including extrusion, heat treatment, and finishing, can contribute to the cost. For example, 6063’s superior extrudability may affect its processing costs compared to 6061.
Market Demand:
- The overall demand for aluminum and specific alloys in the market can influence prices. High demand or scarcity of supply can lead to fluctuations in prices.
Supplier and Location:
- The choice of supplier and their location can impact transportation costs. Local suppliers may offer better prices due to reduced shipping expenses.
Surface Finish and Treatment:
- The surface finish and any additional treatments (anodizing, coating, etc.) can add to the overall cost. Some applications may require additional processing that affects the final price.
Quantity and Customization:
- The quantity of material ordered and any customization requirements can affect pricing. Larger quantities might be eligible for bulk discounts, while customized alloys or specific tolerances may incur additional costs.
Buyers need to obtain quotes from multiple suppliers, considering the factors mentioned above. Additionally, staying informed about market trends and fluctuations in aluminum prices can help in making cost-effective decisions.
In Conclusion:
In conclusion, understanding the unique properties of aluminum 6061 vs 6063 aluminum is critical for various industries.
Aluminum alloy 6061 offers exceptional strength and versatility, making it ideal for structural uses.
Aluminum metal 6063, on the other hand, is known for its excellent extrusion properties and corrosion resistance, making it a popular choice for construction applications.
Choosing the right alloy requires a thorough understanding of its properties and potential uses.
This understanding ensures optimal performance and cost-efficiency in diverse industrial environments.