Definition and Composition: AR400 VS AR500 Steel
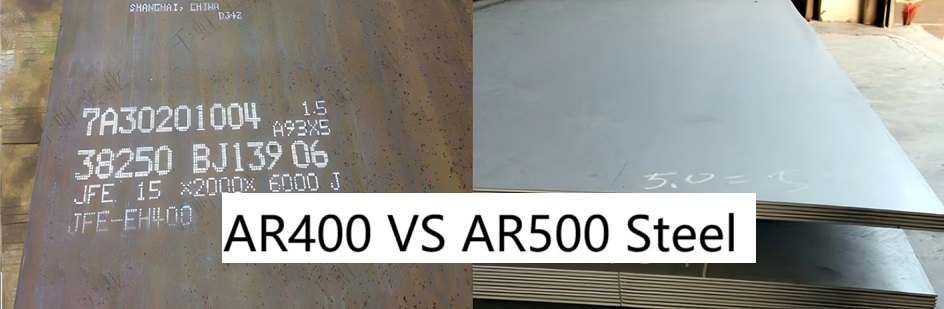
What is AR400 Steel?
AR400 steel is a type of wear-resistant steel that is known for its high hardness and durability. It is specifically designed to resist wear and abrasion caused by contact with rough materials, such as rocks, gravel, ores, and other abrasive substances. AR400 steel is commonly used in applications where the material needs to withstand heavy wear and impact, such as in mining equipment, dump truck bodies, excavator buckets, and conveyor systems.
What is AR500 Steel?
AR500 steel is a type of hardened, wear-resistant steel known for its exceptional toughness and resistance to wear. It is specifically designed to withstand heavy impacts and high levels of abrasion, making it suitable for applications where the material needs to endure extreme conditions.
AR500 steel derives its name from its hardness level, which typically falls within the range of 470 to 540 Brinell Hardness Number (BHN). This high hardness provides superior resistance against penetration, allowing the steel to withstand the impact of projectiles, bullets, and other objects with minimal deformation or damage.
AR400 VS AR500 Steel Composition
C | Mn | P | S | Si | Cr | Ni | Other | |
AR400 Steel | 0.30-0.40% | 1.00-1.50% | 0.025% max | 0.025% max | 0.15-0.40% | – | – | – |
AR500 Steel | 0.30-0.40% | 1.20-1.60% | 0.025% max | 0.025% max | 0.15-0.40% | 0.70-0.90% | 0.20-0.40% | – |
Hardness and Strength: AR400 VS AR500 Steel
AR400 Steel:
- Hardness: AR400 has a hardness range of 360-440 BHN, providing good resistance against abrasive forces.
- Strength: It exhibits excellent impact toughness, making it suitable for applications subjected to repeated impacts.
AR500 Steel:
- Hardness: AR500 steel possesses a hardness range of 470-540 BHN, which offers superior resistance against heavy wear and penetration.
- Strength: Its high hardness provides exceptional resistance to deformation and cracking, making it ideal for high-impact applications.
Applications: AR400 VS AR500 Steel
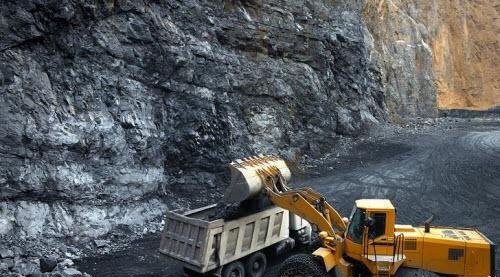
1.AR400 Steel:
- Common Applications: AR400 steel finds application in industries such as mining, construction, agriculture, and forestry.
- Examples: It is used for wear liners, buckets, blades, hoppers, and other equipment exposed to abrasive materials.
2.AR500 Steel:
- Common Applications: AR500 steel is often utilized in industries where extreme wear resistance is required.
- Examples: It is used for targets, armored vehicles, shooting range equipment, and applications involving ballistic protection.
Weldability and Fabrication: AR400 VS AR500 Steel
AR400 Steel:
- Weldability: AR400 steel can be welded using conventional methods, but precautions need to be taken to avoid heat-affected zone (HAZ) issues.
- Fabrication: It can be easily cut, formed, and machined to suit various requirements.
AR500 Steel:
- Weldability: AR500 steel requires special precautions during welding due to its higher hardness and susceptibility to cracking.
- Fabrication: It is more challenging to cut and form compared to AR400, but it can be achieved with appropriate equipment and techniques.
In conclusion
AR400 vs AR500 steels are both excellent choices for applications demanding resistance to abrasion and wear. While AR400 offers a good balance of hardness and toughness, AR500 provides enhanced hardness and penetration resistance. Understanding the differences between these two steels enables industry professionals to select the appropriate material based on specific requirements, ensuring optimal performance and longevity in their applications.
Recommended Articles
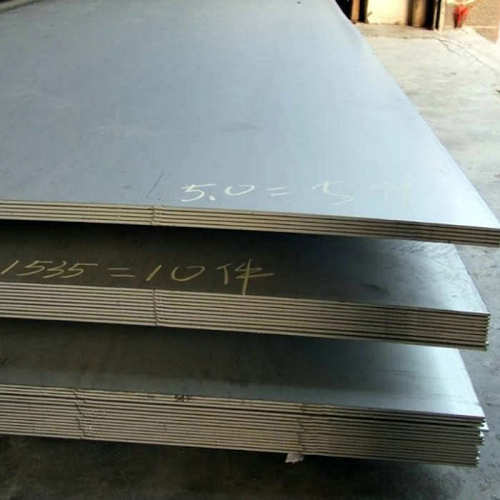
Is AR500 Steel Bulletproof?
As technology continues to advance, people’s concerns about safety are also increasing. In the field of bulletproofing, AR500 steel has attracted much attention due to
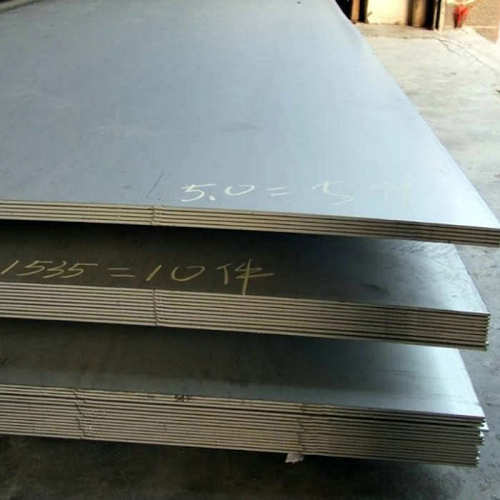
Wear Resistant NM/AR500 Steel Plate
Wear Resistant Steel – NM500 AR500 Steel Plate Our NM500 and AR500 wear-resistant steel plates are designed to cope with extreme wear environments. They have
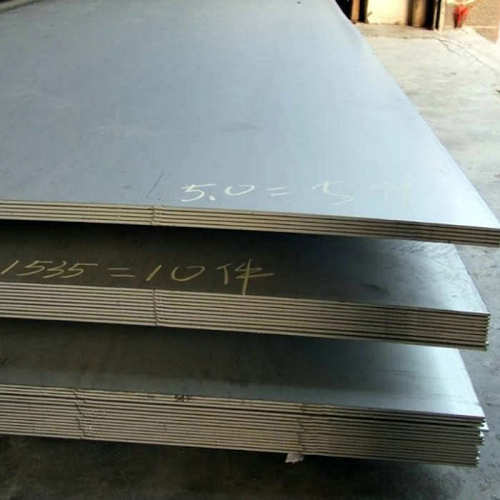
Wear Resistant Steel
Wear Resistant Steel Plate – NM400 NM450 NM500 NM600/AR400 AR450 AR500 AR600 Our range of wear-resistant steel plates (NM400, NM450, NM500, NM600 / AR400, AR450,