When buying aluminum sheet, one of the most common questions is: How thick is 22 gauge aluminum sheet? Understanding gauge measurements is essential to choosing the right aluminum sheet thickness for your project. In this article, we will explain 22 gauge aluminum sheet thickness, its applications, and the importance of choosing a reliable aluminum sheet supplier.
To explore and provide the numerical measurement of 22 gauge aluminum, shedding light on its dimensions and highlighting its relevance in different contexts.
Gauge System and Aluminum Thickness
- Introduction to the gauge system for measuring sheet metal thickness
- Explanation of the inverse relationship between gauge number and thickness
- Emphasizing the utilization of the American Wire Gauge (AWG) system for aluminum
Gauge to Inches Conversion (Common Aluminum Sheet Gauges)
Gauge | Thickness (inches) | Thickness (mm) |
---|---|---|
16 | 0.0508 | 1.29 |
18 | 0.0403 | 1.02 |
20 | 0.0320 | 0.81 |
22 | 0.0250 | 0.64 |
24 | 0.0201 | 0.51 |
26 | 0.0159 | 0.40 |
If you need 22 gauge aluminum sheets, we have them in stock! Contact us now to get the best price!
The Thickness of 22 Gauge Aluminum
Certainly! The thickness of 22 gauge aluminum can be expressed in both inches and millimeters:
- In inches: Approximately 0.0253 inches
- In millimeters: Approximately 0.644mm
These measurements provide an approximate value for the thickness of 22 gauge aluminum.
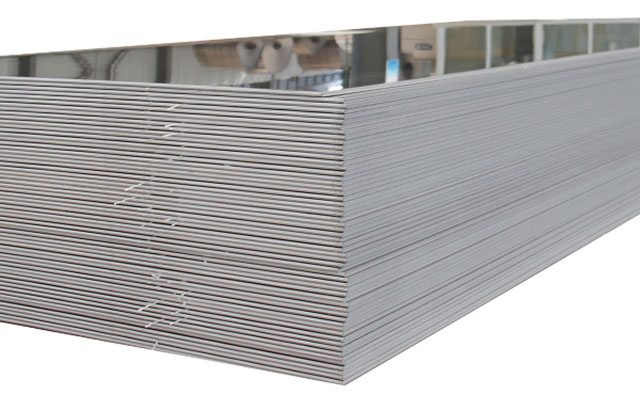
How Thick Is 14 Gauge Aluminum?
Determining the specific thickness of materials is crucial in various industries and applications. In the case of 14 gauge aluminum, understanding its precise thickness provides
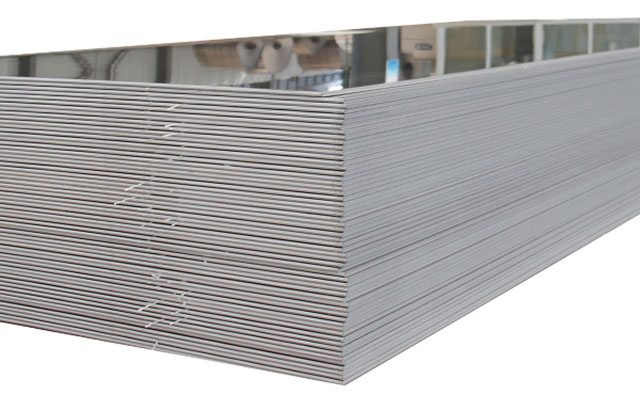
How Thick Is 16 Gauge Aluminum?
Determining the specific thickness of materials is crucial in various industries and applications. In the case of 16 gauge aluminum, understanding its precise thickness provides
Applications and Significance
Roofing and Siding:
Automotive Industry:
The significance of 22 gauge aluminum lies in its combination of properties, including strength, corrosion resistance, lightweight nature, and formability. These characteristics make it suitable for a wide range of applications across different industries, offering durability, functionality, and ease of use.
Need 22 gauge aluminum sheets for your project? Request a quote today!
Engineering and Manufacturing Considerations
When working with 22 gauge aluminum in engineering and manufacturing, several considerations come into play. Here are some important factors to keep in mind:
Strength and Load-bearing Capacity: While 22 gauge aluminum is relatively thin, it still possesses sufficient strength for many applications. However, it’s crucial to assess its load-bearing capacity and structural integrity to ensure it meets the intended requirements. Structural analysis and calculations may be necessary to determine its suitability for specific designs.
Formability and Machinability: 22 gauge aluminum is generally considered to be quite formable, meaning it can be bent, shaped, and formed into various configurations. However, excessive deformation may lead to cracking or loss of structural integrity. It’s important to understand the limits of aluminum’s formability and consider appropriate manufacturing techniques such as bending, rolling, or stamping.
Joining Methods: Joining 22 gauge aluminum parts often involves welding, riveting, or adhesive bonding. Welding methods such as TIG (Tungsten Inert Gas) or MIG (Metal Inert Gas) welding are commonly used, but attention should be paid to preventing distortion or warping due to the thin gauge. Proper surface preparation and selecting suitable filler materials are crucial for achieving strong and durable joints.
Surface Protection and Finishing: Aluminum, including 22 gauge, is susceptible to corrosion. Applying protective coatings or finishes, such as anodizing or powder coating, can enhance its resistance to environmental factors. Pre-treatment processes like cleaning and etching may be required to ensure good adhesion of coatings and finishes.
Material Compatibility: When using 22 gauge aluminum in combination with other materials, it’s important to consider their compatibility. Avoiding galvanic corrosion, which occurs when dissimilar metals come into contact in the presence of an electrolyte, is critical. Proper insulation or the use of compatible materials can prevent this issue.
Thermal Considerations: Aluminum has good thermal conductivity, which can be advantageous or challenging depending on the application. Consideration should be given to thermal expansion and contraction, heat dissipation, and potential thermal stress during manufacturing and operational conditions.
Cost and Availability: Assessing the cost and availability of 22 gauge aluminum is essential during the engineering and manufacturing process. Consider the quantity required, sourcing options, and any specific processes that may affect the material cost.
By taking these engineering and manufacturing considerations into account, designers and manufacturers can effectively utilize 22 gauge aluminum for various applications while ensuring performance, reliability, and cost-effectiveness.
Why Choose 22 Gauge Aluminum?
When selecting aluminum, the gauge thickness impacts the strength, weight, and flexibility of the material. Here are some key advantages of 22 gauge aluminum:
Lightweight & Easy to Work With – Ideal for cutting, bending, and shaping.
Corrosion-Resistant – Excellent for outdoor and marine applications.
Cost-Effective – Affordable for various industrial and personal projects.
Versatile – Suitable for both structural and decorative uses.
Looking for bulk orders? We offer wholesale pricing! Contact us now.
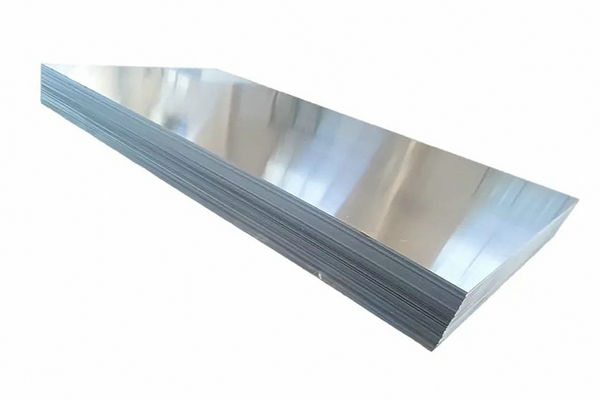
Where to Buy 22 Gauge Aluminum?
If you’re looking for a reliable 22 gauge aluminum supplier, we provide:
High-quality aluminum sheets in different sizes and finishes.
Competitive prices with bulk discounts.
Fast shipping and worldwide delivery.
Custom cutting services to meet your specifications.
Get a Free Quote Today! Simply send us your requirements, and our team will assist you in finding the best aluminum solution for your needs.
In conclusion
22 gauge aluminum typically has a thickness of approximately 0.0253 inches or 0.644 mm. It’s important to note that the gauge measurement system is used to determine the thickness of various materials, including aluminum. The higher the gauge number, the thinner the material.
Need more details or a quote? Contact us today for expert help!