Cutting Copper Tube Options
When it comes to cutting copper tubes, there are a few options you can consider. Here are three common methods:
1. Pipe cutter: A pipe cutter is a specialized tool designed for cutting copper tubes. It consists of a sharp cutting wheel that rotates around the pipe, gradually making a clean and even cut. To use a pipe cutter, follow the steps mentioned in the previous response.
2. Hacksaw: If you don’t have a pipe cutter, a hacksaw can be used to cut copper tubes. Here’s how to do it:
– Measure and mark the desired length on the tube.
– Secure the tube in a vise or clamp to prevent it from moving.
– Place the hacksaw blade on the mark and start sawing back and forth, applying gentle pressure.
– Maintain a steady and even motion until the cut is complete.
– After cutting, use a deburring tool or sandpaper to smooth out any rough edges.
3. Tubing cutter: A tubing cutter is similar to a pipe cutter but is specifically designed for cutting small-diameter copper tubes. It operates in a similar way to a pipe cutter, with a cutting wheel that rotates around the tube. Tubing cutters are often used in tight spaces or for more precise cuts on smaller tubes.
No matter which method you choose, it’s important to measure accurately, secure the tube properly, and take necessary safety precautions such as wearing gloves and eye protection. Additionally, ensure that the cut is clean and free from burrs or sharp edges, which can be removed using a deburring tool or sandpaper.
How To Cut Copper Pipes?
To cut copper pipes, you can follow these steps:
1. Gather the necessary tools: You will need a pipe cutter, which is specifically designed to cut copper pipes, and a deburring tool or sandpaper to smooth the edges of the cut pipe.
2. Measure and mark: Use a tape measure to measure the length you need for your copper pipe. Mark the measurement using a pencil or a marker.
3. Secure the pipe: Place the copper pipe in a vise or use a pipe clamp to secure it firmly in place. Make sure the area you are cutting is accessible and not obstructed.
4. Adjust the pipe cutter: Open the pipe cutter and position it on the marked spot of the copper pipe. Tighten the cutter’s screw or knob to secure it in place. The cutting wheel should be aligned with the mark.
5. Begin cutting: Rotate the pipe cutter around the pipe in a clockwise direction. Apply steady pressure while turning the cutter, making sure the wheel stays aligned with the mark. Continue rotating until the pipe cutter makes a complete revolution around the pipe.
6. Tighten the cutter: After one full revolution, tighten the cutter slightly by adjusting the screw or knob. Repeat step 5, rotating the cutter around the pipe again. Continue tightening and rotating until the pipe is cut. You should feel a slight drop in resistance when the cut is complete.
7. Remove burrs: Once the pipe is cut, use a deburring tool or sandpaper to remove any sharp edges or burrs from the cut end of the pipe. This will ensure a clean and smooth surface.
8. Inspect and clean: Inspect the cut end of the pipe to ensure it is clean and free of debris. You can also use a clean cloth or rag to wipe away any metal shavings or residue.
Remember to wear safety goggles and gloves while working with copper pipes to protect your eyes and hands. Additionally, make sure to follow all safety guidelines and local plumbing codes when working on plumbing projects.
What To Do After Cutting A Copper Pipe
After cutting a copper pipe, there are a few steps you should take to ensure proper handling and installation:
- 1. Inspect the cut: Take a close look at the cut end of the copper pipe to ensure it is clean and free of any burrs or rough edges. If you notice any sharp or uneven areas, use a deburring tool or sandpaper to smooth them out. This will help prevent leaks and ensure a proper connection.
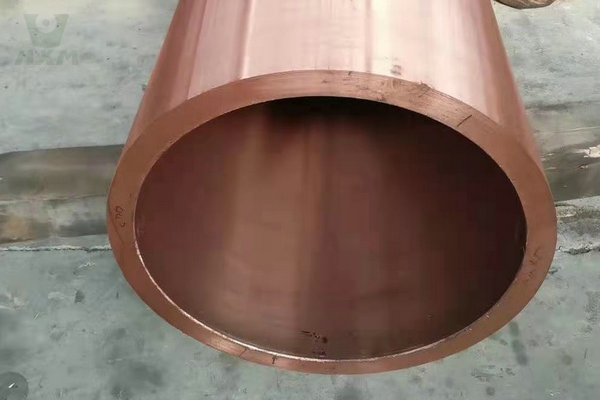
- 2. Clean the cut end: Use a clean cloth or rag to wipe away any metal shavings or debris from the cut end of the pipe. It’s essential to have a clean surface for a reliable and secure joint.
- 3. Prepare for connection: Depending on your specific plumbing needs, you may need to connect the cut copper pipe to another fitting or join it with another pipe. Follow the appropriate steps for the type of connection you require. This may involve soldering, using compression fittings, or other methods as per your plumbing system requirements.
- 4. Flux and solder (if applicable): If you are soldering the copper pipe, apply flux to both the cut end of the pipe and the fitting or joint you are connecting it to. Then, heat the joint with a torch while applying solder to create a strong and watertight seal. Follow the proper soldering techniques and safety precautions.
- 5. Test for leaks: Once the joint is made, allow it to cool and then test for leaks. Turn on the water supply and check for any signs of water seepage or drips. If you notice any leaks, you may need to recheck and redo the connection.
Remember to follow local plumbing codes and guidelines while working with copper pipes. If you are uncertain about any step or the appropriate method for your specific plumbing project, it’s advisable to consult a professional plumber for assistance.