Aluminum foam is a lightweight and versatile material that has gained popularity in recent years for its unique properties and various applications. It is made by introducing a foaming agent into molten aluminum and then allowing the mixture to solidify. The resulting material has a porous and cellular structure, which makes it lightweight, strong, and able to absorb energy.
Aluminum foam is used in a wide range of industries, including aerospace, automotive, construction, and defense, among others. It can be used as a structural material, a heat exchanger, a sound absorber, and a shock absorber, among other applications.
In this article, we will provide a step-by-step guide on how to make aluminum foam. We will cover the materials and equipment needed, the preparation process, the production process, and post-production techniques to handle and store the finished product. We will also discuss the potential applications of aluminum foam and its advantages compared to traditional materials. By the end of this article, you will have a comprehensive understanding of how to make aluminum foam and its potential uses.
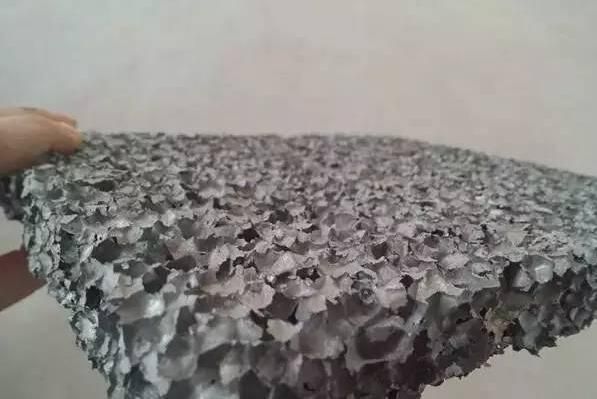
Materials and Equipment of Aluminum Foam
Before starting the production process, there are a few crucial steps to follow to ensure the process runs smoothly:
Safety first: Aluminum powder and foaming agents can be hazardous if not handled correctly. Always wear safety equipment, work in a well-ventilated area, and keep a fire extinguisher nearby.
Prepare the materials: Mix the aluminum powder, foaming agent, fluxing agent, and release agent in the correct ratios as per your recipe.
Prepare the equipment: Clean and prepare your equipment and molds thoroughly to ensure they are free of any debris or contamination.
Assemble the setup: Set up the furnace or gas torch and crucible, ensuring that the thermocouple is in place to measure the temperature accurately.
By following these steps, you will be ready to start the production process with confidence.
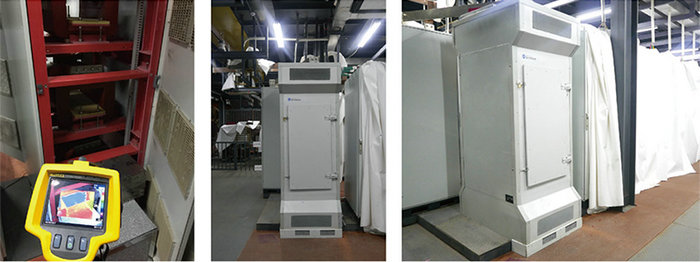
Preparation
Before starting the production process, there are a few crucial steps to follow to ensure the process runs smoothly:
Safety first: Aluminum powder and foaming agents can be hazardous if not handled correctly. Always wear safety equipment, work in a well-ventilated area, and keep a fire extinguisher nearby.
Prepare the materials: Mix the aluminum powder, foaming agent, fluxing agent, and release agent in the correct ratios as per your recipe.
Prepare the equipment: Clean and prepare your equipment and molds thoroughly to ensure they are free of any debris or contamination.
Assemble the setup: Set up the furnace or gas torch and crucible, ensuring that the thermocouple is in place to measure the temperature accurately.
By following these steps, you will be ready to start the production process with confidence.
Production Process
The production process of aluminum foam involves several steps. Here is a step-by-step guide on how to make aluminum foam:
Step 1: Preheat the furnace or gas torch
Before adding any materials, preheat the furnace or gas torch to the desired temperature. The temperature required will depend on the specific materials you are using and the type of foam you want to produce. For example, the temperature range for producing aluminum foam can vary from 700°C to 1000°C.
Step 2: Melt the aluminum
Once the furnace or gas torch reaches the desired temperature, add the aluminum powder or granules to the crucible and allow it to melt. Stir the aluminum occasionally with a stirring rod or paddle to ensure that it melts evenly.
Step 3: Add the foaming agent
Once the aluminum has melted, add the foaming agent to the mixture. The foaming agent will produce gas bubbles, which will expand and create the foam’s porous structure. The amount of foaming agent you add will depend on the specific recipe you are using.
Step 4: Add the fluxing agent
Next, add the fluxing agent to the mixture. The fluxing agent will help to remove any impurities from the aluminum and ensure that the foam has a uniform structure. Again, the amount of fluxing agent you add will depend on the specific recipe you are using.
Step 5: Pour the mixture into molds or forms
Once the mixture is fully mixed and free of impurities, pour it into molds or forms. It’s crucial to work quickly as the mixture will start to solidify as it cools. Make sure the molds or forms are clean and free of any contaminants.
Step 6: Allow the foam to cool and solidify
Allow the foam to cool and solidify in the molds or forms. The cooling time will depend on the specific recipe you are using and the size and shape of the molds or forms. It’s essential to let the foam cool and solidify completely before removing it from the molds or forms.
Step 7: Remove the foam from the molds or forms
Once the foam has cooled and solidified, remove it from the molds or forms. Use a release agent to ensure that the foam doesn’t stick to the molds or forms.
Step 8: Finish the foam
After removing the foam from the molds or forms, you can finish the foam to achieve the desired properties and appearance. This may include sanding, polishing, or coating the foam.
By following these steps, you can successfully produce high-quality aluminum foam. It’s important to note that the specific recipe and production process may vary depending on the application and desired properties of the foam. Therefore, always follow the recipe and guidelines provided by your supplier.
Post-Production
Once the aluminum foam has been produced, it’s essential to handle and store it correctly. Here are some post-production tips to ensure the foam stays in good condition:
Handle with care: Aluminum foam is delicate and can be easily damaged. Handle it with care and avoid dropping it or applying too much pressure.
Store in a dry place: Moisture can cause the foam to corrode or degrade over time. Therefore, store the foam in a dry and cool place.
Clean the foam regularly: Regular cleaning will help to maintain the foam’s appearance and properties. Use a soft brush or cloth to remove any dirt or debris.
Consider finishing techniques: Depending on the application and desired properties, you may want to consider finishing techniques such as coating or polishing the foam.
Dispose of waste correctly: Aluminum foam production generates waste, such as the crucible and any unused materials. Dispose of the waste correctly and follow any local regulations regarding hazardous waste.
By following these post-production tips, you can ensure that the aluminum foam remains in good condition and performs as expected.
Application of Aluminum Foam
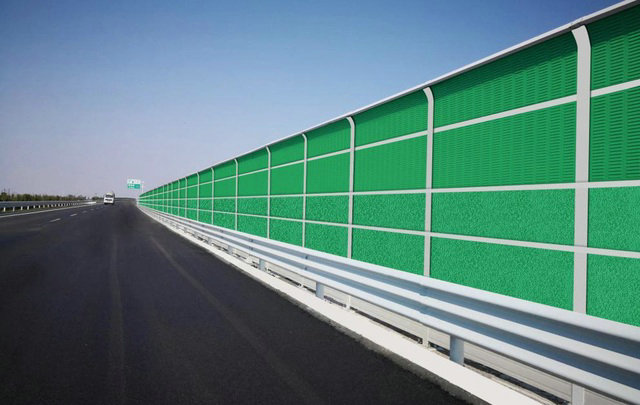
Aluminum foam has a wide range of applications due to its unique properties. Here are some of the most common applications of aluminum foam:
Aerospace industry: Aluminum foam is used in the aerospace industry for lightweight structural components, thermal management, and acoustic insulation.
Automotive industry: Aluminum foam is used in the automotive industry for lightweight crash absorbers, heat shields, and sound insulation.
Construction industry: Aluminum foam is used in the construction industry for building insulation, fire protection, and structural panels.
Defense industry: Aluminum foam is used in the defense industry for blast and impact protection.
Marine industry: Aluminum foam is used in the marine industry for buoyancy and structural components.
Medical industry: Aluminum foam is used in the medical industry for orthopedic implants and prosthetics.
Sports equipment: Aluminum foam is used in sports equipment such as helmets, padding, and bicycle frames due to its lightweight and shock-absorbing properties.
The use of aluminum foam continues to expand, and researchers are exploring new applications and properties of the material. With its unique properties and versatility, the aluminum foam has the potential to transform many industries and improve the performance of products and structures.
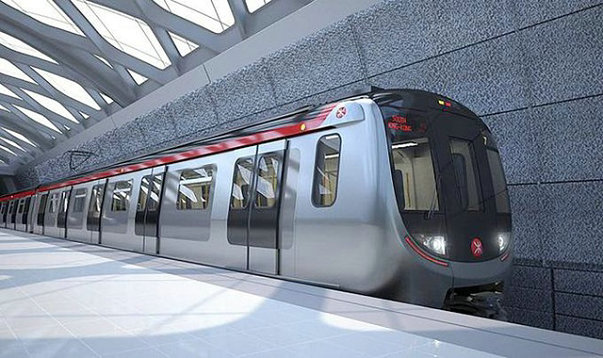
In Conclusion
Lastly, it’s important to note that the production of aluminum foam is a complex process that requires a certain level of expertise. If you are not experienced in handling and working with molten metals, we recommend seeking professional guidance or assistance.
Overall, the production of aluminum foam requires careful planning, attention to detail, and strict adherence to safety precautions. By following the steps outlined in this article, you can successfully produce high-quality aluminum foam with the desired properties and appearance.
We hope that this article has provided you with a comprehensive guide on how to make aluminum foam and its potential applications. By using aluminum foam, you can take advantage of its unique properties and contribute to a more sustainable and efficient future.