Metal Coating is a type of surface treatment, forming a thin film of a metal different from the material on the surface of metal or resin. The Chinese character for “gold plating” can be written as “plating”, “electroplating”, and sometimes “plating”. This time, we will introduce the types and methods of gold plating.
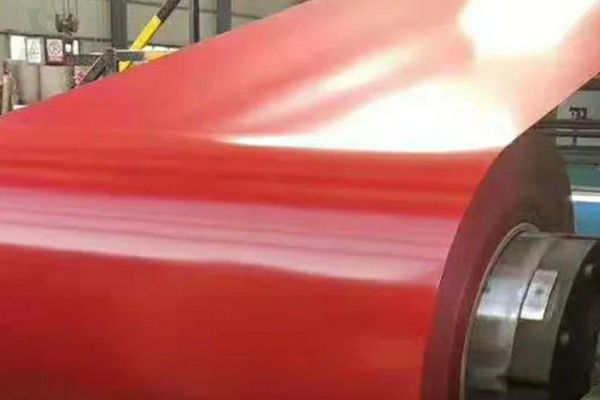
What is Metal Coating?
Plating is a surface treatment that covers the surface of a workpiece that becomes a base with a thin metal film. There are three main purposes of plating.
• Improvement of Decorativeness
Plating is done to improve the aesthetic appearance, such as creating a shiny surface or a high-grade color. Representative examples include gold plating.
• Improvement of Corrosion Resistance
Some materials such as iron commonly used in industrial products are prone to rust. Therefore, the surface is covered with a corrosion-resistant metal, which is plating to avoid rust. Zinc plating is a representative example.
• Improvement of Functionality
In addition to decorativeness and corrosion resistance, plating can also add various functions. For example, in plating to optimize the suitability of solder called solder wettability, nickel plating is performed, or copper and tin alloys are used for plating. In addition, there is plating to improve sliding properties or conductivity.
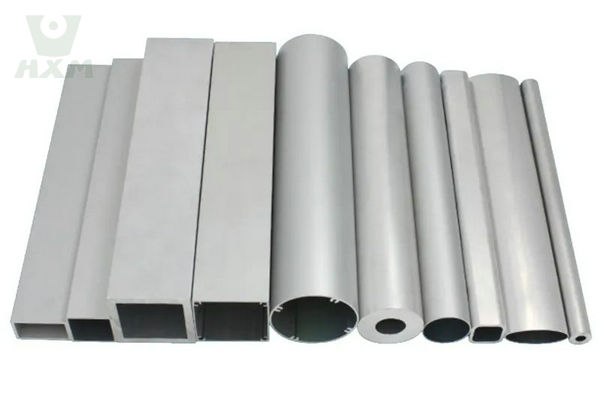
Aluminized Steel
Aluminized Steel Manufacturers | Suppliers in China Aluminized Steel is a type of steel with high corrosion resistance and high heat resistance. It is made
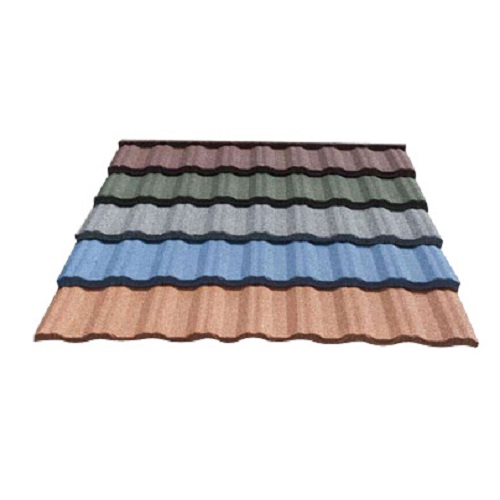
Color Stone Metal Tile
Metal Colored Stone/Rainbow Roof Tiles Manufacturers Our premium metal colored stone and rainbow roof tiles combine modern design with exceptional durability to add a unique
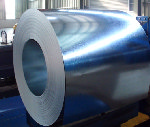
EGI
Electro Galvanized Steel (EGI) Suppliers Electro-galvanized steel, often abbreviated as EG or EGI, is a type of steel that has undergone a special electroplating process

PPGI/PPGL/PPGF
PPGI/PPGL/PPGF Steel Suppliers Are you looking for PPGI/PPGL/PPGF Steel Suppliers? Our company provides high-quality and competitively priced PPGI (pre-painted galvanized steel), PPGL (pre-painted galvanized steel),
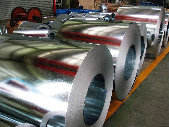
GL/GF
Hot-Dip Galvanfan / Galvalume Steel Suppliers Hot dip galvanizing and galvalume are two different processes used to protect steel from corrosion. They involve applying a
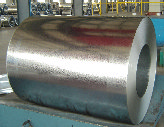
GI
GI Galvanized Steel Coils Suppliers Huaxiao Metal is a leading supplier of galvanized steel sheets and coils. Galvanized steel is defined as carbon steel plated
Types of Plating
There are many types of plating.
*The values listed are for reference only.
Types | Vickers Hardness (HV) | Layer thickness(μm) | Processable materials | Uses | Purpose and Features | Remark | |
Galvanizing | − | 3~20 | Carbon Steel | Thin plate | · Rust-proof, low price · Poor appearance | − | |
Chrome | − | 1~2 | Carbon Steel | Sheet metal parts | · Rust-proof, low price · Suitable for mass production · Decreased aesthetics but can replace nickel plating | − | |
Bright Galvanized | − | 1~2 | Carbon Steel | − | |||
Trivalent Chromates | − | 1~2 | Carbon Steel | Bolts and nuts | · Rust-proof and low-priced · Does not contain hexavalent chromium | − | |
Nickel Plating | − | − | Carbon steel | − | · Improve corrosion resistance and decoration · Chrome plating has better corrosion resistance in the atmosphere | · Copper-based electroplating can be applied as needed · Deeper depressions cannot be applied | |
No. 1 plating | 500 | 5~20 | · The appearance is better than the No. 3 plating | Material → polishing → plating → polishing | |||
No. 3 plating | − | · Material → Plating | |||||
Pear skin plating | − | − | · Fatigue resistance · Small defects are not noticeable | · Material → Pear skin treatment → Plating | |||
Electroless nickel plating | 500 | Ability to specify | Carbon steel | Parts that cannot be nickel-plated | · Easy to manage film thickness · Strong corrosion and wear resistance · Can make non-metallic materials into conductors · Can be cured by heat treatment after plating | − | |
镀铬 | − | − | Carbon steel | − | · Lustrous appearance · Good corrosion resistance · Chrome plating is easy to sinter when sliding against each other | · Nickel-based plating is performed as needed · Deeper depressions cannot be performed | |
No. 1 plating | 500 | 5~20 | · The appearance is better than the No. 3 plating | Material → polishing → plating → polishing | |||
No. 3 plating | − | · Material → Plating | |||||
Pear skin plating | − | − | · Fatigue resistance · Small defects are not noticeable | · Material → Pear skin treatment → Plating | |||
Hard chrome plating | 1000 | 10~30 | Shafts Sliding parts | · Excellent wear resistance · More expensive than other chrome plating | · Material → Plating (No. 3 plating) | ||
Iron trioxide protective film | − | − | Carbon Steel | Bolts | · Paint base · Appearance (glossy) · more prone to rust than diffusion nitriding | · Produce iron(III) oxide (black) | |
Low temperature black | − | 1~2 | Carbon steel | Parts that require precision | · Long-term anti-rust ability · Best corrosion resistance among black colors · Ultra-thin film | · Because it is processed at low temperatures, there is no heat effect on the material, and parts combined with plastics, rubber, etc. can also be processed directly. | |
Anodizing | White | − | 3~5 | Aluminum Alloy | − | · Anti-corrosion and wear resistance · Non-conductive · Heat resistance | There is a coloring anodizing treatment, which forms a hard oxide film on the surface and uses the pores of the oxide film for coloring. |
Plating is roughly divided into three categories based on the processing method. We will explain each of them starting in the next chapter.
Plating and Type
Electroplating is the most common method in plating and is used to make materials decorative, rust-proof, wear-resistant, and conductive. The metal to be plated and the plating metal are placed in a solution containing metal ions, the metal to be plated is connected to the cathode, the plating metal is connected to the anode, and a direct current is passed. Then, a reduction reaction occurs in the solution, and the plating metal is precipitated on the metal surface of the anode.
The amount of metal precipitated changes with the current density, so the thickness of the plating becomes uneven depending on the shape of the part. Specifically, the plating is thicker in protruding parts and thinner in recessed parts. The plating thickness of electroplating changes with the current and time passed, so it is necessary to find the plating thickness that suits the purpose for each plated part.
There are mainly the following types of electroplating.
Gold Plating
Gold is a metal with a beautiful luster, but it is characterized by its high price. Therefore, gold plating is performed to improve decorativeness by covering only the surface of the product with gold. Gold is not only beautiful in appearance, but also chemically stable, so it has excellent corrosion resistance and can also be used for rust prevention and conductivity.
Silver Plating
Silver is also a metal with excellent decorative properties like gold. However, since it is easily oxidized, it is necessary to perform a treatment to prevent discoloration after silver plating. Since it has high conductivity, it is used for surface treatment of connector parts of precision equipment, etc.
Galvanizing
This is the most commonly used processing method for rust-proof plating. When zinc is plated on carbon steel parts, it prevents corrosion of carbon steel due to the self-sacrificing effect on carbon steel. After zinc plating, gloss zinc plating and trivalent chromate gloss treatment are performed to protect the zinc plating layer.
Chromium Plating
Chromium plating is performed to make decorative plating glossy. In addition, it has strong wear resistance and excellent corrosion resistance, so it is also used for mechanical parts in the industrial field.
Electroless Plating and Types
Electroless plating is a plating method that does not use electricity. The product to be plated is immersed in a solution containing metal ions that form a coating, and the metal ions are reduced to form a coating. Since no electricity is used, non-conductors such as resins can also be plated. At this time, since the metal film formed on the surface is conductive, electroless plating is sometimes performed on non-conductor products to make them conductive as a pretreatment for electroplating.
Nickel plating is a common plating method in electroless plating.
Electroless Nickel Plating
This is a plating method also known as chemical nickel plating. The thickness of the coating is more stable than electrolytic nickel plating, but the temperature of the plating solution is higher, so you need to pay attention. Electroless nickel plating has excellent wear resistance and rust resistance.
Other Plating
In addition to electroplating and electroless plating, there are chemical conversion treatments (black oxide film), anodizing treatment (aluminum oxide), hot-dip galvanizing, etc.
Chemical Conversion Treatment (Black Oxide Film)
When you want to obtain a black surface, chemical conversion treatment is used. It is also called blackening treatment, which forms a tetra-trioxide film. The thickness of the film is thin and stable, and it can also be applied to parts with strict dimensional tolerances.
Anodizing Treatment (Aluminum Oxide)
The method of forcibly oxidizing the surface of aluminum materials to obtain a film is called anodizing treatment. It has high hardness and excellent corrosion resistance.
Hot-Dip Galvanizing
Hot-dip galvanizing is the method of immersing parts in a heated and molten solution to form a film on the surface. It is used for wires, structures, etc. Because it is immersed in molten zinc, the influence of heat is greater.
In Conclusion:
Plating is a method of forming a coating of other types of metal on the surface of metal or resin. Plating is performed for various purposes such as improving decorativeness, achieving rust resistance, and durability. In addition to electroplating, electroless plating, which precipitates metal in a solution, is also used.
Huaxiao Metal can provide instant quotes and processing for plating.