Inconel Alloy Supplier and Manufacturer From China
We specialize in providing high-quality Inconel alloys to meet the needs of various industrial applications. Inconel alloy is a nickel-based superalloy known for its excellent high temperature and corrosion resistance. It is widely used in aerospace, chemical processing, power generation, and oil and gas industries. As a leading global Inconel alloy supplier and manufacturer, we not only provide abundant spot inventory but also meet your procurement needs at very competitive prices. Whether you need Inconel alloy plates, bars, or other forms of products, we can provide professional services and fast delivery.
Are you looking for a reliable Inconel alloy supplier, competitive Inconel alloy pricing, or Inconel alloy stock for sale? Contact us today for a quote or learn more about our other alloy products.
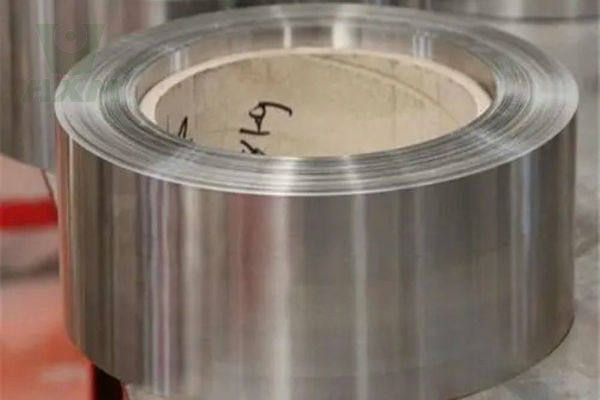
Inconel Alloy For Sale - China Suppliers
Grades: Inconel600, Inconel601, Inconel617, Inconel625, Inconel718, InconelX-750, etc.
Sizes: Custom sizes available
Shapes: Sheet/Plate/Bar/Tube/Strip/Coil/Wire, etc.
Standard: ASTM B166, ASTM B572, AMS 5580, ASTM B167, UNS N07718, etc.
Huaxiao Metal offers competitive pricing for Inconel alloy based on market trends, order volumes and custom requirements. Contact us today for detailed Inconel quotes and bulk purchase discounts.
Inconel Alloy Data Sheet
Equivalent Grades
Inconel 600, Inconel 601, Inconel 617, Inconel 625, Inconel 718, and Inconel X-750 are nickel-based high-temperature alloys known for their excellent oxidation resistance, corrosion resistance, and high-temperature strength. Below is a comparison of their equivalent grades across different international standards:
Alloy | ASTM/UNS (USA) | EN/DIN/W.-Nr. (Europe) | JIS (Japan) | Other Equivalent Grades |
---|---|---|---|---|
Inconel 600 | UNS N06600 | 2.4816 | NCF 600 | W.Nr. 2.4816, NiCr15Fe |
Inconel 601 | UNS N06601 | 2.4851 | NCF 601 | W.Nr. 2.4851, NiCr23Fe |
Inconel 617 | UNS N06617 | 2.4663 | NCF 617 | W.Nr. 2.4663, NiCr22Co12Mo |
Inconel 625 | UNS N06625 | 2.4856 | NCF 625 | W.Nr. 2.4856, NiCr22Mo9Nb |
Inconel 718 | UNS N07718 | 2.4668 | NCF 718 | W.Nr. 2.4668, NiCr19FeNbMo |
Inconel X-750 | UNS N07750 | 2.4669 | NCF X-750 | W.Nr. 2.4669, NiCr15FeTiAl |
Chemical Composition Comparison (%)
Alloy | Ni | Cr | Fe | Mo | Al | Ti | Nb/Ta | Mn | C | Si | Other Elements |
---|---|---|---|---|---|---|---|---|---|---|---|
Inconel 600 | 72 min | 14-17 | 6-10 | – | – | 0.15 max | – | 1.0 max | 0.15 max | 0.5 max | S: 0.015 max |
Inconel 601 | 58-63 | 21-25 | Bal. | – | 1.0-1.7 | – | – | 1.0 max | 0.1 max | 0.5 max | S: 0.015 max |
Inconel 625 | 58 min | 20-23 | 5.0 max | 8-10 | 0.4 max | 0.4 max | 3.15-4.15 | 0.5 max | 0.1 max | 0.5 max | P: 0.015 max |
Inconel 718 | 50-55 | 17-21 | Bal. | 2.8-3.3 | 0.2-0.8 | 0.7-1.15 | 4.75-5.5 | 0.35 max | 0.08 max | 0.35 max | B: 0.006 max |
Inconel X-750 | 70 min | 14-17 | 5-9 | – | 0.4-1.0 | 2.25-2.75 | 0.7-1.2 | 1.0 max | 0.08 max | 0.5 max | B: 0.006 max |
Physical Properties Comparison
Property | Inconel 600 | Inconel 601 | Inconel 625 | Inconel 718 | Inconel X-750 |
---|---|---|---|---|---|
Density (g/cm³) | 8.47 | 8.11 | 8.44 | 8.19 | 8.28 |
Melting Range (°C) | 1354-1413 | 1360-1411 | 1290-1350 | 1260-1336 | 1390-1427 |
Thermal Conductivity (W/m·K) at 100°C | 14.9 | 12.4 | 9.8 | 11.4 | 11.2 |
Electrical Resistivity (μΩ·m) at 20°C | 1.03 | 1.15 | 1.29 | 1.25 | 1.25 |
Specific Heat (J/kg·K) | 444 | 460 | 410 | 435 | 419 |
Coefficient of Thermal Expansion (10⁻⁶/°C, 20-100°C) | 13.3 | 13.7 | 12.8 | 12.6 | 12.8 |
Mechanical Properties Comparison
Property | Inconel 600 | Inconel 601 | Inconel 625 | Inconel 718 | Inconel X-750 |
---|---|---|---|---|---|
Tensile Strength (MPa) | 550 min | 600 min | 830 min | 1035 min | 1265 min |
Yield Strength (MPa) | 240 min | 270 min | 517 min | 725 min | 865 min |
Elongation (%) | 30 min | 25 min | 30 min | 12-19 | 20 min |
Hardness (HB) | 150 max | 160 max | 225 max | 331 max | 360 max |
Modulus of Elasticity (GPa) | 206 | 205 | 207 | 204 | 214 |
Are you looking for a competitively priced Chinese Inconel alloy supplier? Huaxiao Metal specializes in providing high-quality Inconel alloys with excellent heat resistance, corrosion resistance, and mechanical strength.
Our Inconel products are widely used in aerospace, chemical processing, marine, and high-temperature industrial applications. Contact us today for Inconel alloy pricing and stock information!
Inconel Alloy Application
Aerospace: Engine components, turbine blades, and exhaust systems.
Chemical Processing: Heat exchangers, reactors, and processing equipment.
Oil and Gas: Offshore platforms, pipeline systems, and valves.
Power Generation: Turbine seals, combustion liners, and nuclear reactors.
Looking for a reliable Inconel alloy supplier? Contact Huaxiao Metal to purchase premium Inconel bars, plates, tubes, and wires at factory direct prices. We guarantee high quality materials, fast delivery, and professional service.
Request an Inconel alloy quote now and let us be one of your trusted Inconel alloy suppliers!
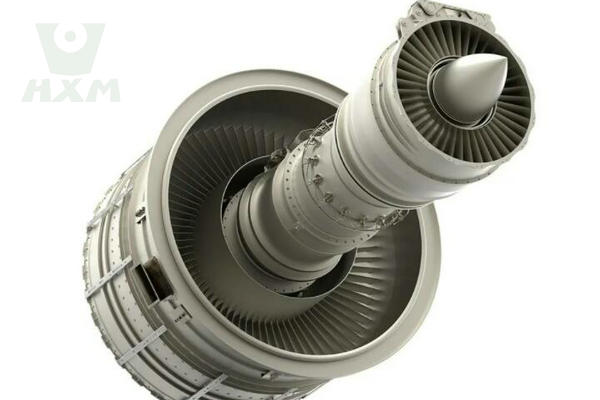
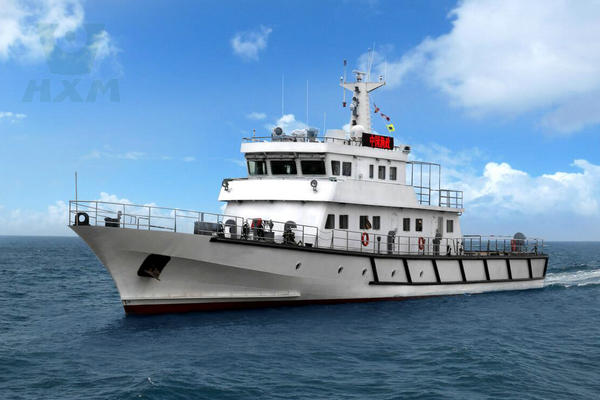
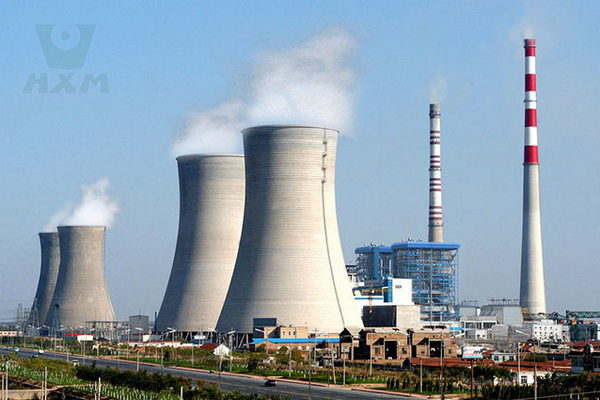
Product Features of Inconel Alloy
Excellent High-Temperature Stability: Inconel alloys can withstand temperatures exceeding 1,000°C (1,832°F) without significant loss of strength.
Superior Corrosion Resistance: Resistant to oxidation, corrosion, and pitting in both aqueous and high-temperature environments.
High Mechanical Strength: Inconel retains its toughness and strength even at elevated temperatures.
Versatile Applications: Commonly used in aerospace, chemical processing, power generation, and oil and gas industries.
If you need further details on product specifications or a price quote, feel free to contact us!
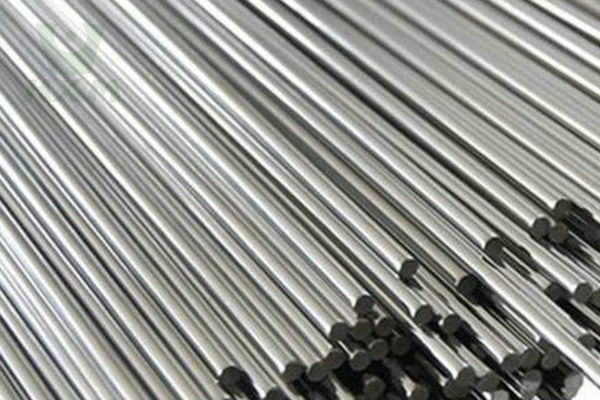
Types of Inconel Alloy
If you are looking for Inconel suppliers with sufficient inventory and fast response, Huaxiao Metal is a good choice. As a professional Inconel manufacturer, we have 600, 625, 718, and other models in stock all year round and can provide material certificates and third-party test reports. Regarding Inconel prices, we support on-demand quotation, Please feel free to contact us for the latest information.
Alloy | Max Temp (°C/°F) | Oxidation Resistance | Corrosion Resistance | Strength | Key Applications |
---|---|---|---|---|---|
Inconel 600 | 1090°C / 2000°F | Excellent | Good | Medium | Chemical processing, heat exchangers, nuclear reactors |
Inconel 601 | 1200°C / 2200°F | Superior | Moderate | Medium | Industrial furnaces, exhaust systems, thermal processing |
Inconel 617 | 1100°C / 2000°F | Excellent | High | High | Gas turbines, aerospace, heat exchangers |
Inconel 625 | 980°C / 1800°F | Good | Outstanding | High | Marine, chemical processing, aerospace |
Inconel 718 | 700°C / 1300°F | Good | High | Very High | Jet engines, power plants, cryogenic storage |
Inconel X-750 | 980°C / 1800°F | Very High | Moderate | High | Turbine blades, nuclear reactors, springs |
If you’re looking for high-quality Inconel alloys, feel free to contact us for a price quote or more details!
FAQ From Huaxiao Metal Supplier
What is Inconel Alloy?
Inconel is a family of nickel-chromium-based high-temperature alloys known for their outstanding resistance to extreme temperatures and corrosion. This alloy group maintains high strength and durability even under harsh conditions, making it an indispensable material for industries that require reliability in high-stress, high-temperature environments.
Common Inconel grades include Inconel 600, Inconel 625, Inconel 718, and Inconel X 750, each suitable for different industrial applications.
As an experienced Inconel manufacturer, Huaxiao Metal has been committed to providing stable and reliable high-temperature alloy materials to customers around the world. We are not only a direct Inconel suppliers, but we also provide additional services such as cutting and forging according to demand. When communicating with customers, we will also provide reasonable Inconel prices according to the current market situation to help customers better control costs.
Contact us now to get the latest Inconel alloy prices and stock information!
Is Monel better than inconel?
Monel and Inconel are both high-performance nickel-based alloys but serve different purposes:
Monel is best known for its superior resistance to corrosion in neutral and alkaline salts and seawater, making it ideal for marine and chemical environments.
Inconel, on the other hand, is renowned for its ability to withstand extreme temperatures and maintain strength under such conditions, making it suitable for aerospace and high-temperature industrial applications. Which alloy is “better” depends on the specific environment and conditions of the application.
Inconel Vs Monel
What causes Inconel to crack?
Inconel alloys, like all materials, can crack under certain conditions:
Thermal cycling: Rapid heating and cooling can lead to thermal expansion and contraction, causing stress and eventual cracking, especially if there are pre-existing flaws.
Creep and stress: Long-term exposure to high temperatures and stress can cause creep (gradual deformation), leading to cracks in the material.
Improper welding: Inconel alloys are susceptible to cracking during welding if the heat treatment process is not properly controlled or if there are excessive thermal gradients.
Hydrogen embrittlement: Exposure to hydrogen, especially during manufacturing or high-temperature operations, can lead to cracking.
Corrosion: Under certain corrosive environments (such as sulfur-bearing gases), Inconel alloys may suffer from localized corrosion, which can initiate cracks.
Is Inconel better than titanium?
It depends on the application. Inconel and titanium both have exceptional high-temperature and corrosion-resistant properties, but they have different strengths:
Inconel is often favored for extremely high-temperature applications due to its excellent resistance to oxidation and creep at elevated temperatures (over 800°C).
Titanium has a higher strength-to-weight ratio and better performance at lower temperatures, especially in aerospace and marine environments.
Titanium is more lightweight than Inconel, making it more suitable for applications where weight is a concern, while Inconel is better for situations requiring strength at extreme temperatures.
Inconel is typically more resistant to oxidation and corrosion in harsh environments like combustion chambers and exhaust systems.
Please click on the link below to learn more about the differences between Inconel and Titanium.
Inconel vs Titanium-The Ultimate Difference Explained
What is the strongest Inconel alloy?
Inconel 718 is generally considered the strongest of the Inconel alloys. It has excellent mechanical properties and high resistance to oxidation and corrosion, making it the material of choice for a variety of high-stress applications, especially in the aerospace and gas turbine industries.
Inconel 625 and Inconel 750 are also high-strength alloys, with Inconel 750 having an advantage in creep strength at elevated temperatures.
Why is Inconel 718 difficult to machine?
Inconel 718 is difficult to machine for the following reasons:
High Hardness and Strength: It maintains strength even at high temperatures, making it more resistant to cutting and wear during machining.
Work Hardening Properties: During machining, the material tends to work harden, making it harder to cut.
Low Thermal Conductivity: This can lead to excessive heat buildup during machining, which can affect tool life and cause material deformation.
Toughness: Its toughness can lead to increased wear on cutting tools, requiring specialized machinery and techniques to achieve precision cutting.
What are the disadvantages of Inconel?
High cost: Inconel alloys are expensive due to the complex alloying elements and the manufacturing process.
Difficult to machine: As mentioned, Inconel alloys, particularly Inconel 718, are challenging to machine, requiring specialized tools and techniques.
Heavyweight: Compared to materials like aluminum and titanium, Inconel alloys are heavier, which can be a drawback for weight-sensitive applications.
Brittleness at low temperatures: Inconel alloys may become brittle at cryogenic temperatures, limiting their use in certain applications like low-temperature piping.
What is the most difficult alloy to machine?
Inconel 718 is often considered one of the most difficult alloys to machine due to its high strength, work-hardening characteristics, and low thermal conductivity. Other difficult alloys to machine include:
Titanium alloys: They are also difficult to machine due to their toughness and high work-hardening tendency.
Tungsten and its alloys: These materials are very hard and wear-resistant, requiring specialized tools.
Hastelloy: Another high-performance alloy that is difficult to machine due to its toughness and strength.
What is the difference between Inconel 718 and Inconel 750?
Inconel 718 is a nickel-chromium alloy with added molybdenum, niobium, and titanium, known for its high strength, corrosion resistance, and ability to withstand high temperatures (up to 1300°F/700°C). It is commonly used in aerospace, gas turbines, and nuclear reactors.
On the other hand, Inconel 750 is a modified version of Inconel 718 designed to increase creep strength and provide better performance in extremely high-temperature environments (up to 1800°F/982°C). It contains higher levels of niobium and molybdenum, which enhance its ability to withstand thermal expansion and provide better high-temperature strength.
Difference: Inconel 750 has higher high-temperature strength and better resistance to creep deformation than Inconel 718, making it more suitable for demanding applications.
Inconel 718 VS Inconel X-750
Get Inconel Alloy Prices From Huaxiao Supplier
Huaxiao Metal has established long-term cooperative relationships with many engineering projects and terminal factories over the years. As a trustworthy Inconel manufacturer, we always insist on controlling quality from the source. Many customers finally choose us when comparing different Inconel suppliers. In addition to the good service, more importantly, our Inconel prices have long-term advantages and high cost performance.